La soluzione per stampaggio a conchiglia Figure 4 di 3D Systems offre a BWT Alpine F1 Team velocità e flessibilità senza precedenti.
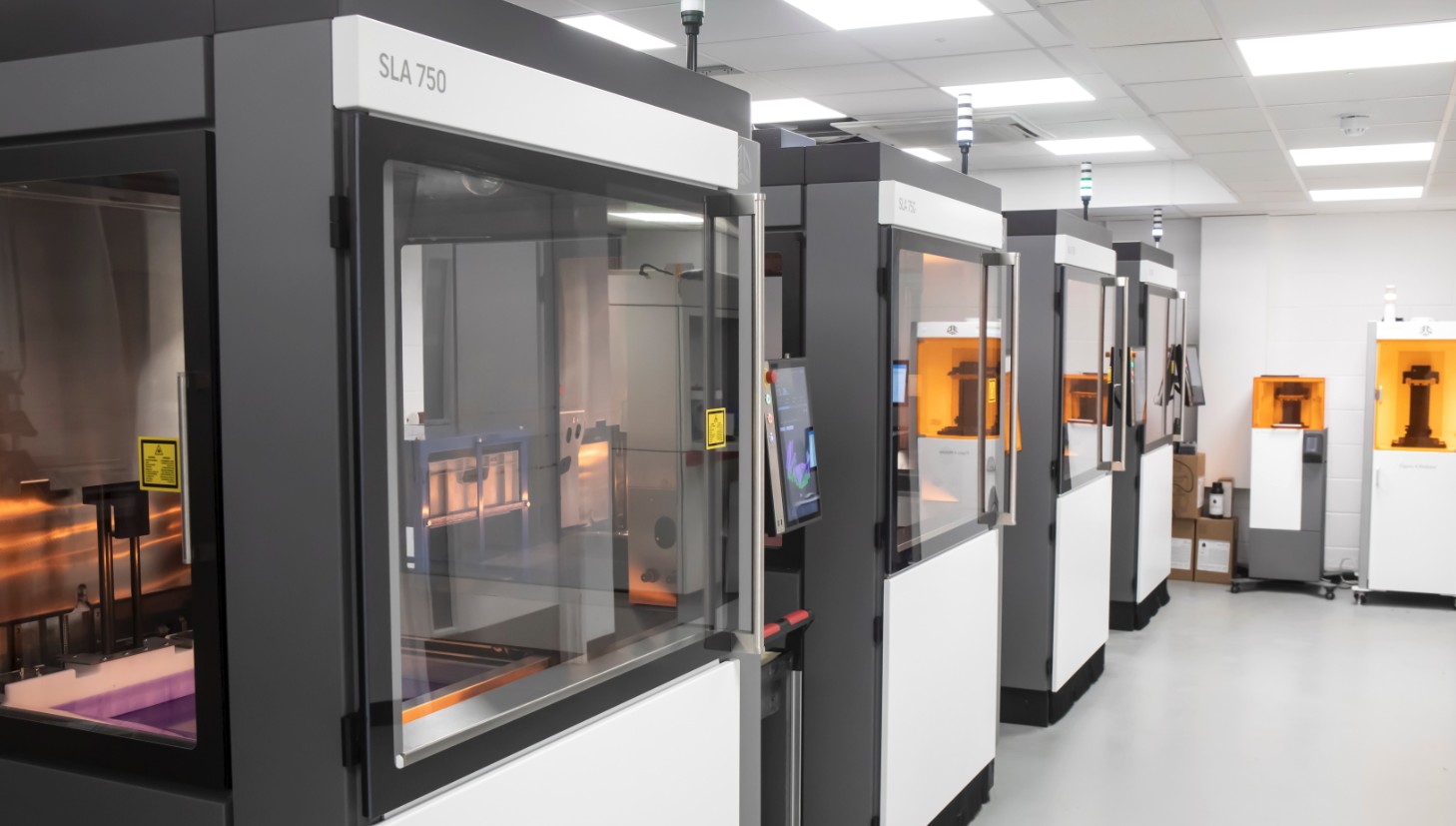
3D Systems ha annunciato l’utilizzo da parte di BWT Alpine F1 Team del materiale Figure 4 EggShell-AMB 10 di 3D Systems per accedere a parti ad alte prestazioni in tempi record.
Arrivare prima
Velocità è la parola d’ordine nelle gare di Formula F1, sia in pista sia per tutto quello “dietro le quinte”. Grazie a Figure 4 EggShell-AMB 10, il F1 Team sta ottenendo velocità di produzione, qualità e flessibilità necessarie per innovare e accelerare lo sviluppo di parti in silicone e poliuretano raggiungendo livelli inediti.
La soluzione per stampaggio a conchiglia Figure 4 di 3D Systems consente a BWT Alpine F1 Team di produrre un ampio ventaglio di parti di alta qualità stampate in silicone e poliuretano in tempi veloci, rendendo possibile, per la prima volta, la creazione di parti uniche e iterative con i materiali per lo stampaggio tradizionale. Il flusso di lavoro semplice si adatta perfettamente al ritmo frenetico della Formula Uno, offrendo al team un vantaggio straordinario. Ad esempio, le rondelle e gli elementi di tenuta, la cui produzione con gli utensili in metallo o la fusione a vuoto tradizionali richiederebbe più giorni o persino settimane, con Figure 4 possono essere consegnati in giornata.
Vantaggi dal materiale
I vantaggi per il F1 Team in termini di produttività vanno ben oltre la produzione di parti in meno di un giorno, ma si traducono anche nella capacità di gestire un ampio ventaglio di applicazioni con il processo di stampaggio a conchiglia di Figure 4. Ciò è reso possibile dal materiale Figure 4 EggShell-AMB 10 di 3D Systems, appositamente ottimizzato per produrre stampi a perdere, che offrono la flessibilità di realizzare parti finali in una vasta gamma di siliconi, poliuretani e altri materiali, quali metalli e ceramiche. Figure 4 EggShell-AMB 10 è una plastica rigida progettata specificamente per resistere all’iniezione a temperatura e pressione elevate, ma facilmente staccabile dopo la fusione.
Flusso di lavoro diretto
Inoltre, il F1 Team esegue più costruzioni al giorno con la stampante 3D Figure 4 Modular per un’ampia gamma di stampi per fusione destinati a componenti delle vetture e alle prove. Secondo Pat Warner, responsabile della produzione digitale avanzata di BWT Alpine F1 Team, la stampa in 3D della maggior parte degli stampi a conchiglia richiede solo 90 minuti, mentre le costruzioni più grandi possono richiedere al massimo 3 ore.
Infine, 3D Sprint di 3D Systems, il software all-in-one per la stampa 3D in polimero, fornisce al F1 Team un flusso di lavoro diretto, dal CAD alla fusione. Il set di strumenti completo comprende opzioni per l’aggiunta di supporti e per la gestione del processo di stampa.
I risultati
«Con queste soluzioni – ha dichiarato Warner – raggiungiamo livelli mai raggiunti finora. Disponiamo di un’immensa gamma di materiali e possiamo utilizzarli praticamente tutti nell’arco di una giornata. Questo consente al team di gestire un ampio ventaglio di applicazioni con proprietà diverse in termini di rigidità, allungamento, colore e altro. Non riesco a immaginare altri modi per produrre così tanti componenti diversi. Le prestazioni richieste ai componenti di Formula Uno sono estreme. Le gare durano fino a 2 ore, durante le quali l’intera vettura è sottoposta a notevoli sbalzi di temperatura, vibrazioni intense e forze estreme. È un ambiente terrificante in cui inserire qualcosa di nuovo, e siamo alla continua ricerca della perfezione. Dobbiamo assicurarci che tutte le parti svolgano la loro funzione secondo le aspettative».
a cura di Redazione
Condividi l'articolo
Scegli su quale Social Network vuoi condividere