Il flusso di lavoro digitale combina la tecnologia Figure 4 e il materiale Figure 4 PRO-BLK 10, passando dal concetto al prodotto finale in massimo 4 giorni.
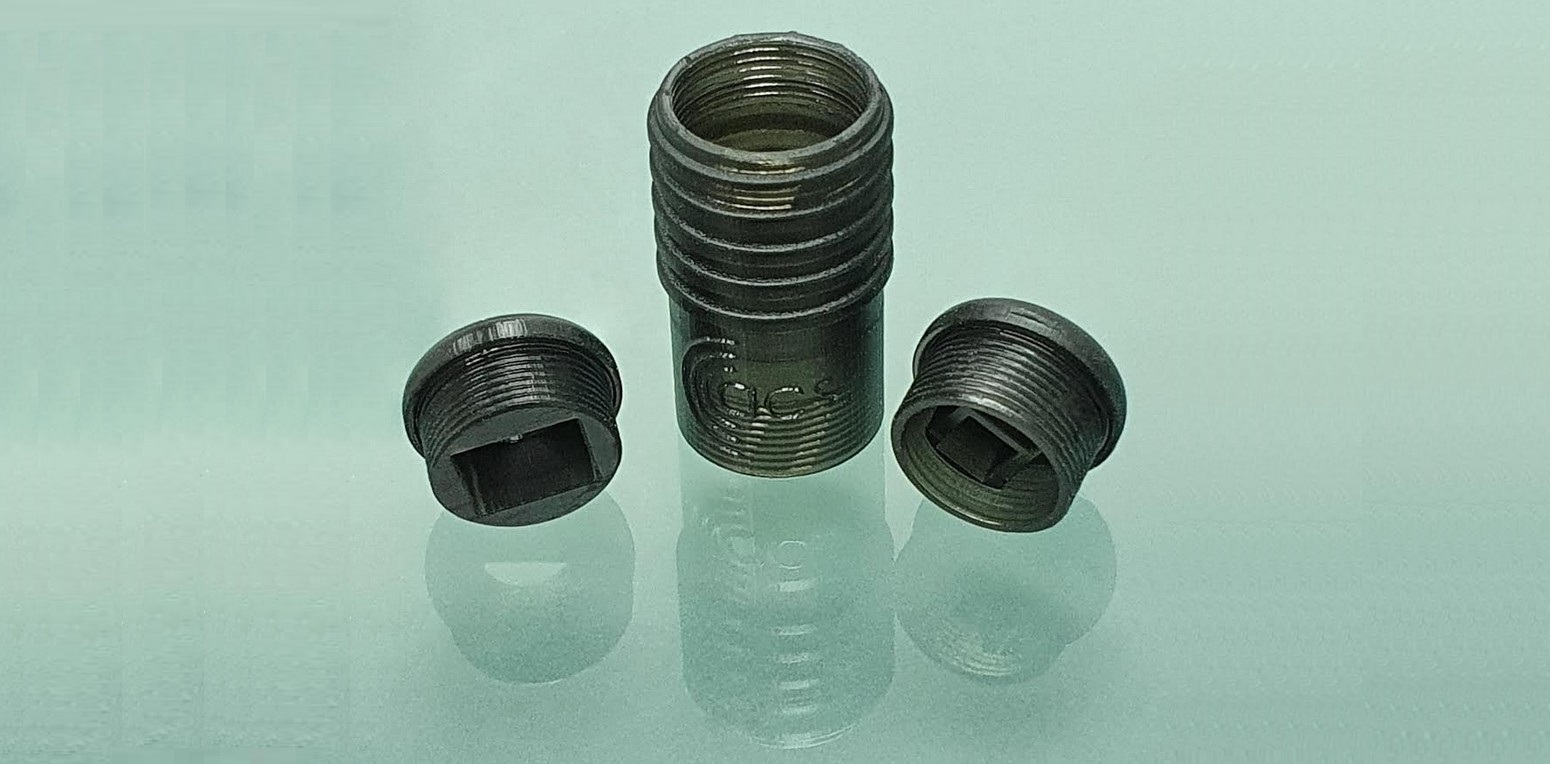
Il flusso di lavoro digitale combina la tecnologia Figure 4 e il materiale Figure 4 PRO-BLK 10, passando dal concetto al prodotto finale in massimo 4 giorni.
L’industria manifatturiera sta vivendo una trasformazione significativa, alimentata dalle potenzialità delle soluzioni di produzione additiva. Un cliente di 3D Systems, la britannica ACS Custom che si occupa della produzione digitale di protezioni acustiche personalizzate, auricolari IEM e altri dispositivi di comunicazione, ha rivoluzionato il proprio flusso di lavoro grazie alla soluzione digitale diretta Figure 4. La soluzione personalizzata di ACS Custom – costituita da Figure 4 PRO-BLK 10, Figure 4 Standalone, il software 3D Sprint e servizi di ingegneria delle applicazioni – sta accelerando il proprio ciclo di sviluppo dei prodotti per offrire un time-to-market più veloce e un vantaggio competitivo. Grazie a questo flusso di lavoro per la produzione digitale diretta, ACS ha quadruplicato la capacità e raddoppiato l’efficienza riducendo, nel contempo, il consumo di materiale del 50% e il costo del lavoro fino all’80%.
«La tecnologia Figure 4 è parte integrante del nostro flusso di lavoro dagli ultimi 2 anni», ha dichiarato Andy Shiach, amministratore delegato di ACS Custom. «Grazie alla collaborazione con il team di 3D Systems, siamo stati in grado di massimizzare il ruolo della tecnologia nel nostro business e la nostra azienda ha raggiunto un livello completamente nuovo. La soluzione unica è stata progettata appositamente per la nostra applicazione e ci ha aiutato ad aumentare notevolmente la capacità e l’efficienza produttiva, nonché a migliorare l’impareggiabile finitura superficiale che consente di fornire prodotti di alta qualità ai nostri clienti».
ACS ha costruito il suo business intorno a un flusso di lavoro completamente digitale che fornisce ai clienti un accesso rapido ad articoli unici nel loro genere. Il team di 3D Systems ha lavorato a stretto contatto con il team di ACS Custom per comprendere le loro specifiche esigenze applicative che hanno portato a una soluzione di produzione digitale diretta. Il fulcro di questa soluzione è il materiale Figure 4 PRO-BLK 10 di 3D Systems, il primo fotopolimero dell’azienda per la produzione additiva che vanta comportamenti termoplastici, fornendo una combinazione di velocità, precisione, resistenza e durata precedentemente associata solo alla produzione con stampaggio a iniezione. Questo materiale ha proprietà uniche e convincenti che garantiscono miglioramenti significativi nella resa della prima stampa, nella deflessione termica, nella stabilità UV, nella durata, nella flessibilità e nella resistenza all’impatto, consentendo inoltre nuovi flussi di lavoro di produzione digitale biocompatibili e diretti, come quello progettato per ACS. Le proprietà del materiale Figure 4 PRO-BLK 10, ovvero la biocompatibilità conforme agli standard ISO 10993-5 e ISO 10993-10, consentono di realizzare un dispositivo a lunga durata che offre una migliore trasmissione e una maggiore qualità del suono. ACS Custom sta utilizzando la stampante 3D Figure 4 Standalone di 3D Systems per passare dal concetto al prototipo, fino al prodotto finale. La piattaforma Figure 4 si adatta perfettamente a questi tipi di applicazioni di produzione personalizzata che richiedono un completamento rapido. La combinazione di Figure 4 PRO-BLK 10 e Figure Standalone consente una velocità di stampa rapida fino a 62 mm/ora con uno spessore dello strato di 50 micron per garantire nuovi livelli di produttiva ad ACS.
Figure 4 Standalone include anche 3D Sprint, un software per la produzione additiva all-in-one che consente l’ottimizzazione dei file, la preparazione e la stampa con una serie di funzioni avanzate per la progettazione, la correzione dei file, l’analisi e molto altro ancora. «3D Sprint è molto intuitivo in termini di layout e le funzioni riguardanti i supporti sono davvero valide», ha spiegato Dan Bennett, direttore tecnico in ACS Custom. «Quando la qualità della superficie esterna è importante, possiamo ridurre la dimensione dei punti di contatto e posizionare i supporti in modo estremamente preciso. In questo modo siamo in grado di creare un prodotto finale confortevole per il cliente».
Oltre che per le applicazioni di produzione diretta, ACS Custom utilizza le stampanti 3D per la fusione in conchiglia. Questa tecnica sfrutta la possibilità di stampare pareti ultrasottili con Figure 4 per creare stampi per l’iniezione di silicone con il materiale Figure 4 EggShell-AMB 10. In seguito all’iniezione, lo stampo 3D può essere rotto e staccato facilmente; ne risulta una parte in silicone che ACS Custom sottopone quindi a post-elaborazione, revisione e finitura. «L’approccio all’innovazione delle soluzioni 3D Systems incentrate sul cliente è alla base di tutto ciò che facciamo, dalla comprensione del flusso di lavoro e dell’applicazione del cliente fino allo sviluppo completo della soluzione», ha dichiarato Scott Anderson, VP e responsabile del segmento di produzione e prototipazione in 3D Systems. «Questo approccio fortemente orientato al mercato offre al nostro team l’opportunità di realizzare applicazioni uniche per ogni cliente e di fornire soluzioni che promuovono la loro innovazione e il valore del cliente a un livello superiore. La nostra collaborazione con ACS Custom mostra come la soluzione Figure 4 (hardware, software e materiali) consente la produzione digitale diretta e indiretta per aumentare l’efficienza, la capacità e la flessibilità, offrendo nel contempo una qualità superiore del prodotto finale. Ciò rafforza il modo in cui le soluzioni di produzione additiva possono davvero garantire un vantaggio competitivo».
Nella foto in alto, un adattatore di comunicazione a 2 pin per cuffie in-ear prodotto da ACS utilizzando la soluzione di produzione digitale diretta Figure 4 di 3D Systems: la parte comprende un corpo centrale e 2 tappi terminali, uno dei quali ospita una presa stereo da 3,5 mm, mentre l’altro include contatti a molla per essere usato con il connettore a due pin della radio. Nelle parti è stampato un filo metrico a passo molto fine: le parti sono funzionali senza alcuna post-elaborazione speciale o taglio del filo.
a cura di Loris Cantarelli
Condividi l'articolo
Scegli su quale Social Network vuoi condividere