Con l’aiuto di Staufen Italia vi proponiamo un approccio in 4 step per la digitalizzazione dei processi aziendali sfruttando i principi della Lean Production. L’obiettivo? Realizzare la miglior combinazione possibile di persone, processi e tecnologie che crei il maggior valore, riducendo il lead time, migliorando qualità ed efficienza.
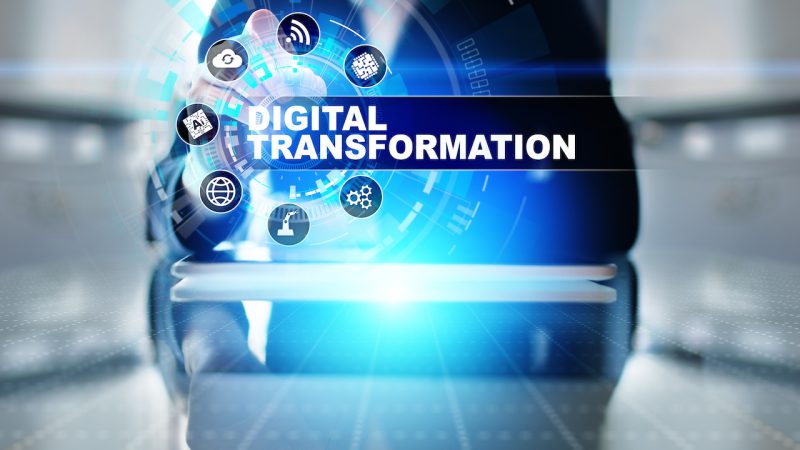
Digitalizzazione dei processi aziendali sfruttando la Lean Production: è questa la strada corretta verso la digital transofrmation. Il tema della digitalizzazione, come sappiamo, è sempre più centrale nel mondo industriale.
Ormai da qualche anno sono molto diffusi annunci dei diversi vendor che pubblicizzano la loro soluzione miracolosa, “utile a digitalizzare i tuoi processi aziendali”.
Farsi irretire da questo approccio, guidato dalla prospettiva di un risultato straordinario piuttosto che da un reale problema o da un potenziale di miglioramento, è fatto comune, perché si vuole perseguire la moda del momento, la soluzione di cui tutti parlano; si brama l’innovazione fine a sé stessa, volendo essere tra i primi a sperimentarla; si teme di non stare al passo di altre aziende del settore, che hanno adottato una o più soluzioni prima di noi (fear of missing out).
Digitalizzazione dei processi aziendali sfruttando la Lean Production
Da dove si deve partire, dunque, per evitare queste insidie e affrontare la digitalizzazione sfruttando la Lean Production?
In un’azienda manifatturiera (ma lo stesso vale per qualsiasi azienda, anche di servizi), le persone devono concentrarsi esclusivamente sulla creazione di valore lungo l’intero processo di evasione degli ordini. L’obiettivo è dunque quello di realizzare la miglior combinazione possibile di persone, processi e tecnologie che crei il maggior valore, riducendo il lead time, migliorando la qualità, l’efficienza, ecc.
Essendo l’azienda un’organizzazione che gestisce informazioni per raggiungere i propri obiettivi, è chiaro quanto sia importante il ruolo delle tecnologie digitali. Dovrebbe però essere chiaro anche quanto queste ultime debbano essere funzionali agli obiettivi e ai processi e non essere un “must have” per definizione.
In tal senso parliamo di Smart Factory, intendendo (perlomeno nella terminologia di Staufen) una combinazione di Lean e Digitale, che consenta di aumentare il valore generato lungo la Value Stream, anziché digitalizzare gli sprechi.
I sette sprechi digitali
Un valido approccio per individuare le possibili aree di intervento è quello di cercare, lungo il processo di evasione degli ordini – il principale processo aziendale insieme allo sviluppo del prodotto – e la value stream, dove sono presenti i cosiddetti “Sette Sprechi Digitali”:
Ridondanza dei dati: questo spreco si genera quando uno stesso dato non segue la regola aurea secondo la quale deve essere inserito a sistema da chi lo genera, una volta, ed essere disponibile a tutti in un unico punto; così si evitano lavori inutili (imputazioni multiple) e soprattutto il rischio di avere dati diversi in punti di diversi del sistema;
Qualità dei dati insufficiente, in quanto porta spreco di tempo a chi li analizza e a potenziali decisioni errate;
Inserimento manuale dei dati, caratterizzato da un elevato impiego di tempo, un alto tasso di errore e significativi ritardi rispetto agli eventi fisici a cui sono correlati;
Isolamento di mezzi e sistemi, creati per scopi specifici e con difficoltà ad integrarsi e scambiarsi dati in tempo reale e che portano nuovamente ad uno spreco del tempo di chi li trasferisce;
Comunicazione cartacea di informazioni non aggiornate, spesso scritte in un primo momento su carta e solo successivamente inserite manualmente nel sistema impiegando più tempo rispetto ad inserirli direttamente nel sistema;
Overflow di dati, che arrivano in numero sovrabbondante rispetto alle necessità dei singoli invece che essere identificati e veicolati in base a ruoli e necessità;
Raccolta e analisi dei dati non sistematiche, spesso non comparabili tra momenti diversi e che danno origine ad indicatori calcolati diversamente e a potenziali decisioni errate basate su essi.
Approccio per Use Cases
Una volta individuati gli sprechi lungo il nostro processo di generazione di valore per il cliente sorge spontanea una domanda: come affrontare il problema?
Un possibile approccio è quello di cogliere queste opportunità e di sviluppare, in piccoli gruppi inter-funzionali, per ognuna di esse uno “use case”, ovvero singole applicazioni di una o più tecnologie che, in combinazione all’esistente panorama di dati e sistemi, ottimizzino un processo tecnologico o organizzativo.
Per poter essere utile in un contesto di approccio passo-passo dell’azienda alla digitalizzazione, ciascun “use case” dovrebbe:
-avere una chiara definizione di quali sono lo scopo ed il perimetro e contemporaneamente di cosa invece è da considerarsi out of scope;
-considerare una o più tecnologie alla base dell’ecosistema Industria 4.0 che interagiscono per realizzare l’applicazione;
-partire da una chiara focalizzazione sui benefici;
-essere collocato al livello dei processi, usando la tecnologia come mezzo per uno scopo.
Per come lo abbiamo definito, questo strumento è limitato nella sua complessità e dunque obbliga a concentrarsi su alcuni aspetti della digitalizzazione in contesti applicativi ben definiti. Questo permette a tutte le persone coinvolte di identificarsi con la soluzione sviluppata e i relativi benefici, ma è anche un prerequisito per immaginare una maggiore complessità da discutere e raggiungere tramite le successive iterazioni.
Recuperare la visione d’insieme
Una volta sviluppati i singoli potenziali progetti, è il momento di trovare un metodo per strutturare una visione d’insieme, che ci aiuti nel processo decisionale attraverso un metodo composto da quattro passaggi chiave.
Il primo di questi consiste nel definire i criteri per valutare sia l’impatto che il costo (monetario e non) di ciascuna soluzione. Tra gli impatti possiamo decidere ad esempio di considerare la produttività, il lead time, la qualità, la flessibilità o l’affidabilità della data di consegna. Tra i costi, oltre a quelli monetari per hardware e/o software, possiamo invece considerare per esempio, le giornate del personale IT interno necessarie, le risorse necessarie oppure il gap di competenze degli utilizzatori e la conseguente necessità di formazione ed addestramento.
Il terzo e il quarto passo verso la digitalizzazione
Per avere un unico valore per impatto e costo delle singole soluzioni, dovremmo decidere il peso delle singole componenti di valutazione, per poter così comparare facilmente i diversi “use case” secondo queste due variabili.
Per poter arrivare al terzo passo, quello della valutazione dei singoli progetti per ognuna delle variabili decise nel primo passaggio, è necessario prima condividere all’interno del gruppo tutti i casi che si andranno a valutare, al fine di dare a tutti gli stessi elementi necessari.
Il quarto e ultimo passo è quello di farsi aiutare dalla matrice benefici-costo per identificare i progetti da inserire all’interno della roadmap, dando la precedenza a quick wins e grandi progetti e cercando di trovare i punti in comune tra quelli selezionati.
Questo sembra essere l’approccio giusto per affrontare la digitalizzazione dei processi aziendali sfruttando la Lean Production.
(a cura di Staufen Italia)
a cura di Simona Recanatini
Condividi l'articolo
Scegli su quale Social Network vuoi condividere