I processi a letto di polvere di metallo sono ideal per realizzare dispositivi medici altamente personalizzati, ma ci sono delle insidie quando si stampano parti utilizzando la SLM (fusione laser selettiva). La convalida virtuale aiuta a stabilizzare il processo per alcune parti per evitare questi errori prima della produzione e migliorare l’efficienza del processo.
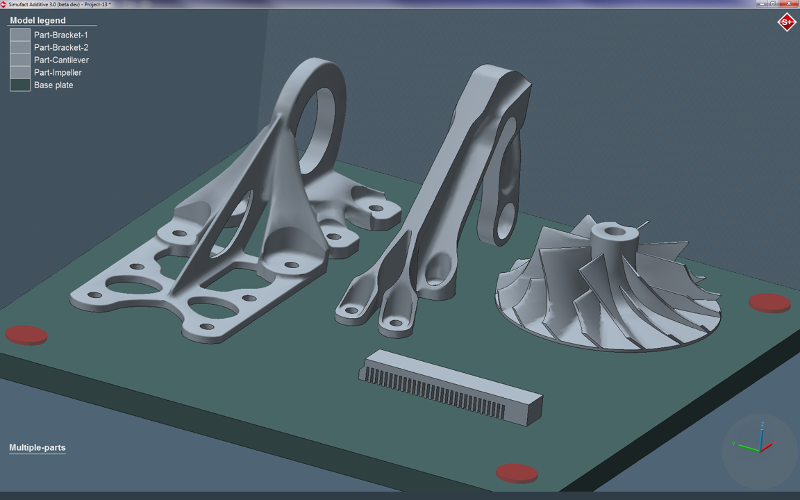
I processi a letto di polvere di metallo sono ideal per realizzare dispositivi medici altamente personalizzati, ma ci sono delle insidie quando si stampano parti utilizzando la SLM (fusione laser selettiva). La convalida virtuale aiuta a stabilizzare il processo per alcune parti per evitare questi errori prima della produzione e migliorare l’efficienza del processo.
La domanda di polvere di metallo è decollata nel 2019 (con una crescita del fatturato del 40% su base annua, secondo The Wohlers Report) e la produzione di dispositivi medici è in prima linea con macchine che funzionano 24 ore su 24, 7 giorni su 7 e spesso sostituiscono completamente i metodi tradizionali. I flussi di lavoro degli impianti medici sono l’incarnazione di nuovi flussi di lavoro agili basati sui dati, in cui un chirurgo che cura un paziente è in grado di personalizzare il trattamento ed eseguire interventi chirurgici che cambiano la vita entro una settimana, ma questa esigenza di impianti di alta qualità che vengono consegnati in pochi giorni richiede fiducia in qualità di stampa.
La progettazione di dispositivi medici richiede la capacità di produrre geometrie su misura per il corpo umano, specialmente quando il dispositivo è in vivo (all’interno del corpo). Un progettista CAD può creare facilmente una rappresentazione digitale di un cubo di Rubik che può essere convertito in un modello ingegneristico con strumenti CAE (Computer Aided Engineering), ma la definizione della geometria dell’anatomia umana di solito inizia con la scansione MRI del paziente.
La produzione additiva è ideale per impianti personalizzati per il paziente. Non sono necessari strumenti costosi e i chirurghi hanno molta libertà di produrre geometrie complesse e ottimizzare la topologia del dispositivo. Inoltre, le polveri di titanio tipicamente utilizzate sono biocompatibili, e offrono un’elevata resistenza se stampate in modo efficace. La qualità e il tempo di consegna sono fondamentali per gli impianti e non è raro che un produttore stampi tre parti in modo da poter scegliere l’impianto di migliore qualità da spedire. Esiste un imperativo di reputazione e di costo per eliminare le distorsioni e altri difetti comuni nei processi SLM e aumentare la fiducia che gli impianti siano corretti la prima volta.
Praticità di produzione
Nei processi SLM, una polvere di metallo fine viene fusa strato per strato utilizzando un laser. La piastra di base viene spostata di conseguenza verso il basso in modo da poter applicare un ulteriore strato di polvere di circa 20-100 μm. Le decisioni pratiche sul processo di preparazione della costruzione possono influenzare notevolmente la stabilità dimensionale della parte finale e la velocità e il costo di produzione. Ad esempio, quando si stampa una singola parte, può essere vantaggioso posizionarla orizzontalmente per garantire una stampa veloce e risparmiare sui costi della macchina. Laddove più parti possono essere prodotte insieme, è preferibile il posizionamento orientato verticalmente per ottimizzare l’utilizzo dello spazio di costruzione, che in genere è solo 250 mm per 250 mm per SLM.
È comune che gli impianti medici abbiano geometrie e filigrane complesse e queste richiedono l’aggiunta di strutture di supporto. Applicando l’ottimizzazione del processo di costruzione, è possibile ridurre l’uso di strutture di supporto per ridurre gli sprechi e ridurre al minimo le fasi di post-elaborazione. L’integrazione dei flussi di lavoro può fornire vantaggi immediati, ad esempio la simulazione del processo Simufact Additive (nella foto in alto, l’ottimizzazione dell’orientamento della stampa all’interno dello spazio di costruzione con Simufact Additive di MSC Software, in quella in basso un impianto cranio-maxillo-facciale secondo metodi computazionali efficienti per prevedere ritiri, deformazioni e tensioni residue) può scambiare dati con Materialise Magics o creare direttamente le sue strutture di supporto più comuni.
Una misura perfetta richiede pazienza
Migliore è la conoscenza del processo e dei dati disponibili, più facile è fare un passo indietro, prevedere il risultato e mitigare i problemi. In SLM, l’applicazione ripetitiva di nuovi strati di materiale caldo che successivamente si restringono porta a una distorsione globale rispetto alla geometria desiderata. Inoltre, vengono generate tensioni residue che possono accumularsi fino al punto in cui compaiono crepe e possono crescere durante il processo di fabbricazione.
Oggi, la maggior parte dei processi AM richiede anche successivi processi di finitura per tagliare la parte dalla piastra di base e rimuovere le strutture di supporto. Questi processi devono essere considerati come parte del flusso di lavoro AM, poiché possono provocare distorsioni le quali implicano che una parte devia dalla geometria finale richiesta. Le geometrie a parete sottile e in filigrana possono essere particolarmente suscettibili alla distorsione, a seconda del loro orientamento e il design della preparazione e del processo di costruzione determina la sua estensione. Utilizzando strumenti di simulazione del processo come Simufact Additive, ambiente di simulazione per l’ottimizzazione “al primo tentativo” dei processi di additive manufacturing a letto di polvere sviluppato da MSC Software, il know-how integrato consente di prevedere in anticipo l’effetto delle sollecitazioni e progettare un processo che eviti la distorsione nella fase di preparazione della costruzione.
Condizioni locali improprie possono portare a difetti su microscala come pori o una mancata coesione che indeboliscono la parte localmente e possono favorire guasti durante la produzione o in servizio. Andando avanti, aspettatevi di vedere processi ulteriormente ottimizzati per fornire risultati di alta qualità con la convalida degli strumenti di scansione di TC (Tomografia Computerizzata) che forniscono CAD completamente digitalizzato per confronti di geometrie stampate. L’ispezione all’interno di un impianto o di un dispositivo medico è essenziale per la garanzia della qualità oggi, ma in futuro l’applicazione di tali dati come feedback per la simulazione del processo aumenterà la precisione del modello e consentirà flussi di lavoro digitali più intelligenti.
a cura di Loris Cantarelli
Condividi l'articolo
Scegli su quale Social Network vuoi condividere