Il case study Stain per l’open house Silgan Dispensing Systems Vicenza.
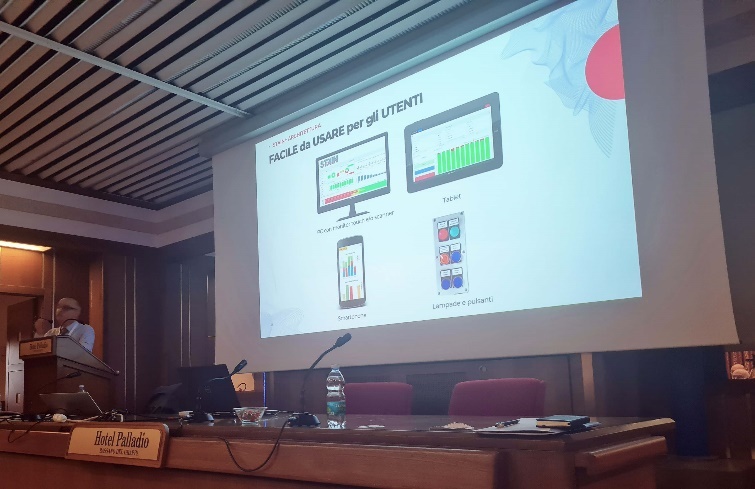
Giovedì 23 Marzo 2023 si è tenuta l’open house Silgan Dispensing Systems Vicenza, presso lo stabilimento della multinazionale specializzata in prodotti di erogazione. Un’iniziativa organizzata da Lutech Stain dedicata a manager, imprenditori e operatori nell’ambito manifatturiero, per far toccare con mano i vantaggi della digitalizzazione dei reparti produttivi e scoprire le soluzioni Mes che hanno permesso a Silgan Dispensing Vicenza di diventare una vera e propria smart factory.
Il pomeriggio è iniziato con un meeting di presentazione dell’azienda e del progetto Mes e si è conclusa con la visita vera e propria agli stabilimenti produttivi.
Assieme a Claudio Morbi (CEO di Lutech Stain), Antonio Riso (Manufacturing Leader di Lutech), Giuseppe Cante e Francesco Rossi (attuale ed ex Operations Manager Silgan Dispensing Vicenza) ed Ermanno Carbone (Plant Manager di Silgan Dispensing Systems Vicenza) si sono ripercorse le tappe del progetto Mes con Stain, dagli obiettivi iniziali, al commitment, fino ai vantaggi raggiunti fino a oggi.
Che cos’è un MES?
Claudio Morbi (nella foto in alto), CEO di Stain, azienda specializzata nello sviluppo di software Mes, di recente entrato a far parte del gruppo Lutech, ha tenuto una breve introduzione sul sistema Mes, e su come esso possa avere impatto sulla gestione della produzione.
Per Morbi il Mes significa “Avere dati alla stessa velocità dei pezzi che produciamo e alla stessa precisione”. Il Mes permette di ottenere le informazioni sul processo produttivo necessarie a comprenderne eventuali problematiche e, quindi, è la base per ottimizzare la produzione. Con questa finalità, il Mes collega il sistema gestionale degli uffici o ERP (Enterprise Resource Planning) alle macchine presenti nei reparti, leggendo direttamente dai sistemi di controllo di queste ultime eventuali fermi e l’andamento della produttività.
Per avere un concreto impatto sulla gestione della produzione, secondo Morbi il Mes deve avere queste caratteristiche: una standard, deve essere facile da utilizzare dall’operatore, i dati devono essere facili da consultare. Ma prima di implementare un sistema di questo tipo, come vedremo nel case study Silgan, è necessario avere una filosofia aziendale orientata al dato come base del miglioramento. In questo Silgan rappresenta un esempio virtuoso.
Se utilizzato con la giusta metodologia, il Mes può dare vantaggi non solo in termini di efficienza (riduzione degli scarti, riduzione tempi di fermo macchina, aumento rendimento velocità, esatta attribuzione dei costi di ciascun articolo se integrato a ERP) ma anche per quel che riguarda la conservazione del know-how produttivo, importantissimo nelle delicate fasi di passaggio generazionale tra figure tecniche.
Di recente Stain è entrata a far parte del gruppo Lutech. Antonio Riso (nella foto qui sotto), Manufacturing Leader del Gruppo, ha confermato che Lutech, uno dei principali system integrator in Italia (466 milioni di fatturato con 3000 professionisti impiegati) con l’acquisizione di Stain ha sicuramente fatto in bel passo all’interno del mondo produzione.
La filosofia di Stain si sposa molto bene con la mission di Lutech, ovvero fornire conoscenze e soluzioni end to end: non solo prodotti ma soluzioni integrate. «E questo è particolarmente importante nel mondo manufacturing – ha notato Riso – dov’è fondamentale avere un approccio concreto con il cliente». Stain in questo senso va a completare l’offerta per il manufacturing di Lutech, che oggi contiene soluzioni Analytics, ERP, SCM, APS, MOM, IOT, Cybersecurity Platform, augmented reality, CAD, PLM.
Silgan Dispensing Sistems Vicenza
Silgan Dispensing Systems Vicenza fa parte di una Holding che ha sede in Connecticut, ha un fatturato annuale di 5 miliardi di dollari e circa 110 plant dislocanti nel mondo. Silgan si propone sul mercato come partner a 360° per la produzione di articoli per packaging. Silgan Dispensing è la divisione che si occupa nello specifico della produzione di articoli per l’erogazione ed il dosaggio per il settore cosmesi, home and garden, personal care e medicale, con plant dislocati principalmente in USA, Europa, Sudamerica e Far East. I suoi principali prodotti sono dispenser, nebulizzatori per profumi, trigger sprayer, attuatori per aerosol, sampler per profumi, tappi dosatori e per aerosol. Nello specifico il plant di Vicenza si inserisce nel segmento trigger; oggi conta più di 270 operatori, una vasta aerea produttiva dotata di un ampio parco di presse di stampaggio ed assemblatrici adatte a soddisfare le richieste produttive anche più complesse, potendo vantare una capacità produttiva di centinaia di milioni di articoli, con migliaia di referenze. Tra i propri clienti Silgan Dispensing Systems Vicenza annovera alcuni tra i più importanti e noti marchi del segmento Home & Garden, che vanno dalle multinazionali ai produttori specializzati in specifici settori professionali. Come ha affermatp Ermanno Carbone, Plant Manager di Silgan Dispensing Vicenza, una complessità produttiva che oggi con il Mes Stain si riesce a monitorare e gestire.
La storia
Il Plant di Vicenza, che celebra 50 anni quest’anno, in origine era un’azienda locale specializzata in prodotti professionali, che via via si è ampliata fino ad arrivare nel 2005 a brevettare uno spruzzatore tutto in plastica molto leggero ed ergonomico. Grazie a importanti investimenti in ricerca e sviluppo, tecnologia, impianti e spazi produttivi, si è imposta sul mercato fino a diventare così appetibile da essere acquistata nel 2010 dalla public Company MWV, che a sua volta in seguito si fuse con RockTenn dando origine a WestRock. Nel 2017 l’azienda viene acquisita dalla Holding Silgan, e da allora non ha mai smesso di investire in ricerca, tecnologia ed innovazione puntando anche sulla sostenibilità dei propri prodotti e processi.
Gli obiettivi del progetto
Gli articoli prodotti da Silgan Dispensing Vicenza sono trigger sprayer prevalentemente in plastica, molti dei quali completamente riciclabili. Articoli apparentemente semplici ma che nascondono molte complessità. Inoltre, come abbiamo visto, man mano che l’azienda cresceva, aumentando il numero di macchine e dei pezzi prodotti, aumentava anche la complessità della produzione e diventava sempre più necessario dotarsi di un sistema di monitoraggio dei processi davvero efficace ed efficiente.
In particolar modo nel 2011 ci fu un ulteriore forte incremento degli investimenti, con un aumento importante della capacità produttiva. Francesco Rossi, l’allora Operations Manager, ha spiegato: «Avevamo clienti importanti che chiedevano giustamente garanzia del rispetto puntuale dei tempi di consegna. Per poter soddisfare le richieste, diventava necessario migliorare il sistema Mes esistente per monitorare la produzione. Da lì emerse l’esigenza di passare ad un sistema Mes più evoluto e versatile ed ebbe inizio il progetto con Stain».
Commitment
A novembre 2013 il Mes Stain viene installato negli stabilimenti di Milano e Vicenza, i primi mesi servirono all’Operations Manager per formare gli operatori e abituarli a utilizzare il nuovo sistema, di cui percepirono subito i vantaggi, primo tra tutti quello di non dover compilare scomodi report cartacei.
Dal gennaio 2014 il sistema viene messo a regime e utilizzato: «Raccogliendo dati – ha proseguito Rossi – ci siamo presto resi conto che le criticità non erano nel reparto stampaggio, che come ci aspettavamo, bensì nel reparto assemblaggio. Infatti a fine 2014, conteggiando in automatico le micro fermate, di cui prima non avevamo percezione esatta – anche perché i tempi ciclo per assemblare un prodotto finito con 10- 12 componenti sono davvero molto spinti – abbiamo quantificato numerose micro fermate, individuando delle inefficienze che, se risolte, ci avrebbero poi permesso, come accadde, di migliorare l’efficienza produttiva senza dover necessariamente investire subito in ulteriore capacità produttiva».
«Questo ci ha permesso di individuare le criticità, mettere in atto azioni correttive e aumentare notevolmente l’efficienza, abbiamo ridotto tantissimo anche gli scarti dello stampaggio, riducendoli a valori realmente trascurabili. L’unico modo per arrivare a simili risultati è quello di dedicare tempo al progetto, ad analizzare i dati. Solo se si misura è possibile migliorare, ma per farlo serve coinvolgere le persone e fare un corretto deployment dei dati a tutti i livelli», ha concluso Rossi.
Il progetto Stain nel 2016 è stato implementato con il modulo MTZ per la manutenzione, e già nel 2017 l’azienda si era certificata a tutti gli effetti Industria 4.0.
I vantaggi di Stain
Giuseppe Cante, attuale Operations Manager, entrato in azienda nel 2015, oggi racconta i vantaggi della raccolta e analisi del dato di produzione con il Mes: «Con Stain abbiamo sempre lavorato fianco a fianco per lo sviluppo dei progetti. Nel 2017 ottenere la certificazione Industria 4.0 per noi è stato un passaggio naturale, avevamo già adottato una filosofia Lean da diversi anni».
Nel dettaglio, l’attuale Operation Manager ha spiegato i benefici apportati dal software Mes Stain per la raccolta dati di produzione, ovvero PRD+: primo tra tutti il monitoraggio produzione, che permette di avere report precisi quotidiani e mensili su singola data/singola pressa. «In questo modo è possibile indire brevi riunioni quotidiane con i capi reparto, per discutere di eventuali criticità emerse. Avere un dato preciso permette di risparmiare tempo per individuare eventuali problemi e risolverli, è uno stimolo per tutti a migliorare».
PRD+ apporta innumerevoli vantaggi anche per quanto riguarda la gestione operativa, perché il sistema invia ordini alle linee stampaggio/assemblaggio, e acquisisce dati della schedulazione. Ultimo ma non meno importante l’analisi dei fermi, che stimola attività di problem solving e identificazione delle causali impattanti.
«In sostanza, il Mes permette di attaccare le problematiche in maniera veloce e incisiva. In Silgan ragioniamo solo in base ai numeri, solo i numeri mettono d’accordo tutti. Essi consentono di avere un processo fluido e definito, identificando causali dettagliate per individuare subito le problematiche, è sufficiente una mezzora al giorno con i capireparto per analizzare i dati e individuare azioni correttive».
Oggi «gli indici di efficienza superano il 95% per lo stampaggio e l’80% per assemblaggio, che è un ottimo risultato considerando le notevoli capacità produttive degli impianti installati». Il modulo MTZ+ di Stain per la gestione della manutenzione è un software che si basa sui dati di produzione e che li elabora in modo da gestire anche i calendari della manutenzione. «Uno dei benefici più tangibili di questo applicativo è che il sistema Mes con MTZ+ permette di avere registrato tutto, e in caso di audit questo è un aspetto fondamentale, in quanto dimostra di avere sotto controllo il processo».
I principali vantaggi del MTZ+ per la manutenzione sono: gestione piani manutenzione e quindi calendario manutenzione, evidenza della esecuzione delle manutenzioni; gestione magazzino ricambi: scarico ricambi, integrazione con magazzino automatico; gestione asset aziendali: inventario completo di macchine, attribuzione dei costi. «Tutti questi aspetti hanno portato ad una riduzione notevole dei costi della manutenzione», ha concluso Cante.
Serve prima di tutto una cultura del dato
Morbi, che ha seguito centinaia di progetti di digitalizzazione della produzione con il Mes, ha affermato che «prima di tutto per impostare un processo di raccolta ed elaborazione dati serve un forte commitment aziendale e obiettivi chiari, perchè la tecnologia è un grande supporto ma da sola non può fare tutto. Serve la volontà di misurare, e di mettersi in discussione per mettere in atto azioni correttive e migliorative».
Carbone ha aggiunto che «è importantissimo formare e sensibilizzare le persone coinvolte nel processo, non solo i manager, ma anche gli operatori».
Cante ha proseguito: «Serve la capacità di mettersi in discussione partendo dai dati. Ogni criticità e ogni obiettivo deve essere rappresentato da un numero, da un gap da colmare. Stain è protagonista di questo processo».
Il Plant Tour
Durante il tour, i partecipanti hanno potuto visitare gli stabilimenti produttivi Silgan Dispensing Systems Vicenza (nella foto in basso, il reaprto stampaggio). Il più recente è stato aggiunto nel 2020, quando c’è stato un importante ampliamento dell’area produttiva. Questa operazione è stata gestita facilmente, senza stop della produzione, come ha notato Carbone, «grazie anche al controllo dei dati e dei processi attraverso il software Stain». Carbone, Rossi e Cante hanno mostrato come vengono raccolti e storicizzati i parametri standard dalle presse (temperature, tempo ciclo, velocità, pressione), per individuare facilmente le cause dei guasti e prevenirli in futuro.
Nei reparti si è potuto vedere in tempo reale tramite gli Andon lo stato di ogni macchina, e chi stava operando in quel momento: un modo per responsabilizzare gli operatori a fare sempre meglio. Sugli Andon viene inoltre proiettata anche una schermata che permette anche di aver il dato a consuntivo storico, per avere un raffronto costante. Vengono infine segnalati i cicli di manutenzione scaduti, in modo da poter ottimizzare al massimo in tempi della manutenzione.
a cura di Redazione
Condividi l'articolo
Scegli su quale Social Network vuoi condividere