Oggi la tendenza di tutte le componenti dell’automazione è quella di rendere i sistemi “autonomi”, in grado cioè di percepire ciò che avviene intorno a loro ed agire senza l’intervento di un operatore. Dalla manutenzione predittiva alle produzioni auto-configurabili la digitronica ha davanti a sé una sfida storica: rendere le macchine autosufficienti.
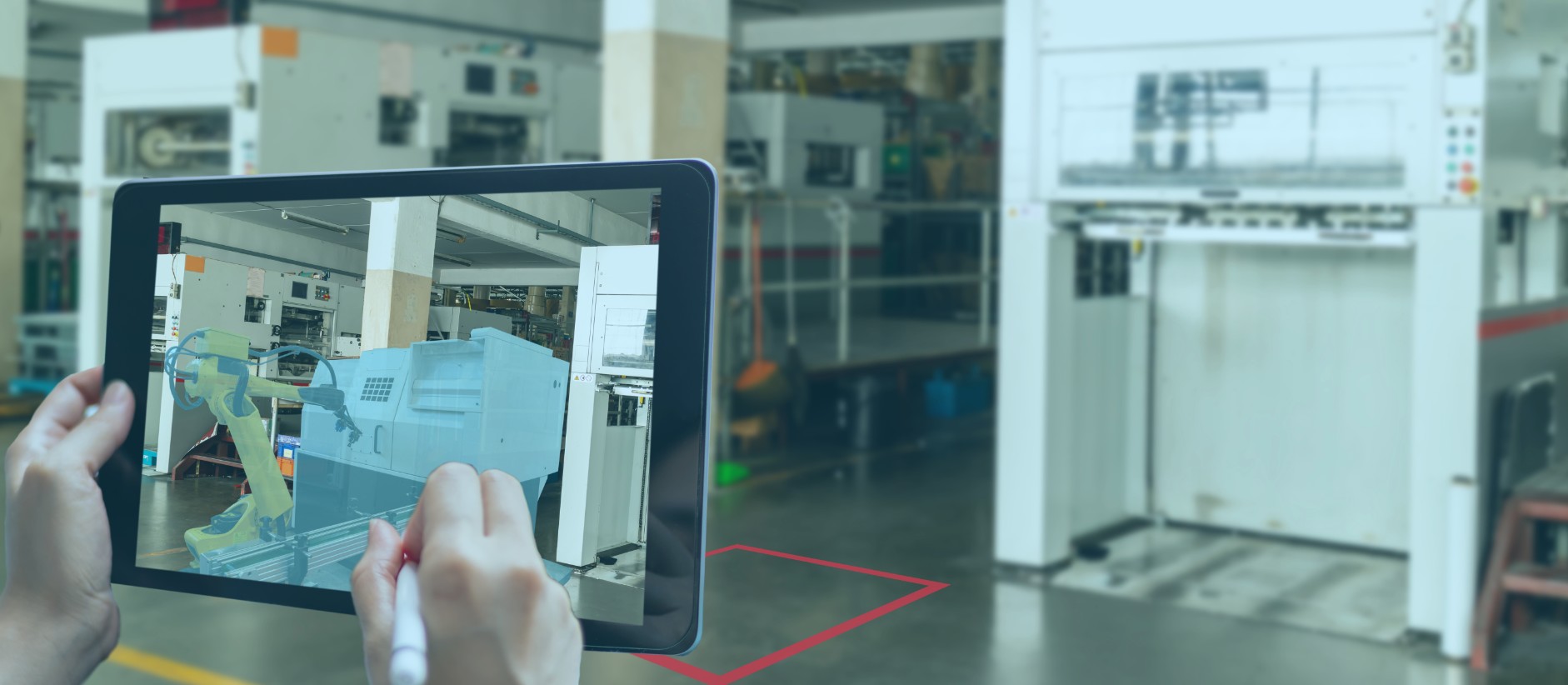
Oggi la tendenza di tutte le componenti dell’automazione è quella di rendere i sistemi “autonomi”, in grado cioè di percepire ciò che avviene intorno a loro ed agire senza l’intervento di un operatore. Dalla manutenzione predittiva alle produzioni auto-configurabili la digitronica ha davanti a sé una sfida storica: rendere le macchine autosufficienti.
di Giambattista Gruosso *
* Dipartimento di Elettronica ed Informazione del Politecnico di Milano
La meccatronica è una disciplina “antica” del mondo dei sistemi automatici e delle macchine utensili. Antica se pensiamo che ha ormai più di 50 anni di vita: nella sua accezione tradizionale si intende la combinazione di meccanica ed elettronica e il termine fu coniato nel 1971 da Tetsuro Mori, un ingegnere della Yaskawa. L’automazione e la meccatronica sono due facce della stessa medaglia e vivono ogni anno che passa delle micro-rivoluzioni dovute all’adozione e alla integrazione di tecnologie sempre più innovative che portano a dei profondi cambiamenti necessari ad affrontare nuove sfide. Fino a diventare loro stesse tecnologie abilitanti in scenari industriali differenti e con una prospettiva di interconnessione a livello di bus di comunicazione sempre più spinta: per cui si può a ragione parlare di digitronica o mutuando da altre lingue, di sistemi ciberfisici.
Fino a oggi, siamo stati abituati a pensare che le tecnologie abilitanti fossero singoli dispositivi o singoli strumenti software: IoT, big data, sistemi di controllo e così via. Ma lo sguardo deve andare oltre questa definizione di tecnologia abilitante. Le macchine ed i sistemi sono diventati essi stessi dei sensori in grado di raccogliere informazione dal mondo esterno e non solo dai componenti interni alla macchina. Questo rende le macchine capaci di elaborare informazioni e nello stesso tempo dare origini a fabbriche o sistemi più complessi, dove gli elementi chiave dell’industria 4.0 sono integrate perfettamente nel macchinario. Queste nuove tecnologie riguardano sicuramente il processo produttivo ma trovano un grande impiego anche nel prodotto stesso, dove meccanica, elettronica e informatica convergono permettendo funzionalità sempre più innovative. Il punto chiave è la capacità di “attuare” sistemi meccanici e nello stesso tempo renderli sensorizzati ed intelligenti fino a fargli raggiungere un’autonomia decisionale. Si parla tanto di veicoli a guida autonoma, ma oggi la tendenza di tutte le componenti dell’automazione e rendere i sistemi “autonomi”, in grado cioè di percepire ciò che avviene intorno a loro ed agire senza l’intervento di un operatore. Dalla manutenzione predittiva alle produzioni auto-configurabili la digitronica (o meccatronica digitale) ha davanti a sé questa sfida: rendere le macchine autosufficienti.
Nuovi scenari sempre più smart
La novità principale rispetto alla meccatronica tradizionale è che lo scenario di riferimento è fortemente cambiato: i temi della smart manufacturing e dell’Industria 4.0 sono diventati più familiari e nello stesso tempo iniziano ad esserci delle soluzioni implementate degne di nota e di approfondimento. Non dimentichiamo poi che la recente pandemia sta cambiando velocemente le condizioni al contorno e sta quindi accelerando diversi processi: la visione è infatti quella di sistemi integrati dove le macchine colloquiano fra loro e con i sistemi centralizzati, dove si simula di più e si “sperimenta” di meno per fare in modo che gli operatori possano lavorare in sicurezza e anche in modalità remota o “smart”. L’industria del futuro si fonda proprio su questa interdisciplinarità: si va dai sistemi meccanici (elementi meccanici, macchine, macchine di precisione), ai sistemi elettronici (microelettronica, elettronica di potenza, tecnologia dei sensori e degli attuatori) fino alle tecnologie informatiche (automazione, teoria dei sistemi, ingegneria del software e l’intelligenza artificiale).
Il sistema nervoso di questa integrazione è la connettività, ruolo svolto in modo egregio dai bus di campo, che consolidano la loro posizione e nello stesso tempo ampliano la loro gamma estendendo le potenzialità anche attraverso le tecnologie dell’Internet industriale. L’IIoT (Industrial Internet of Things) diventa quindi una nelle nuove frontiere dei sistemi meccatronici, con tutto quello che rappresenta. Si può quindi dire che i concetti propri dell’automazione vengono sempre di più influenzato dai concetti che vengono dal mondo del digitale con l’apertura verso sistemi cloud proprietari con capacità di analisi e predizione delle performance e dello stato di salute del sistema che si basano su algoritmi di intelligenza artificiale. Ed è proprio l’intelligenza artificiale, anche integrata nei sistemi meccatronici, una delle frontiere più promettenti: un sistema “digitronico” è dotato di tre caratteristiche principali che sono la capacità di misurare e osservare, la capacità di calcolo e quella di attuazione. Queste ultime due sono oggi molto più performanti rispetto a qualche anno fa, per cui è possibile dotare i sistemi, non solo di semplici logiche di funzionamento, ma anche di elaborate funzioni di calcolo in grado di prevedere comportamenti o di permettere la collaborazione tra macchine differenti. La velocità di calcolo dei processori e la riduzione dei costi fa sì anche la misura indiretta incrementi le sue prestazioni e diventi uno strumento trainante del panorama meccatronico. I sistemi di visione sono infatti al centro di questo processo di trasformazione perché da un lato abilitano misurazioni sempre più efficaci e veloci, dall’altro permettono l’aumento di informazioni che possono essere aggiunte per creare sistemi meccatronici aumentati.
L’apparato “digitronico” stesso porterà dentro di sé tutte le informazioni necessarie alla suo funzionamento e questi sistemi potranno interagire scambiandosi informazioni e suddividendosi il lavoro, anche dal punto di vista del calcolo e del controllo. In altre parole non si parla di costruire solamente un sistema nervoso attraverso l’impiego di tecnologie abilitanti come quelle che vengono dal mondo dell’informatica, ma anche creare una forma di intelligenza distribuita che faccia diventare i processi autonomi ed in grado di autoregolarsi. I sistemi digitronici hanno davanti a sé anche questa sfida: saper sfruttare al massimo le performance di calcolo dei sistemi moderni per svolgere funzioni sempre più complesse e articolate.
Superare la mera connettività dei sistemi
Si tratta di mettere in rete tra di loro questi sistemi, dove per mettere in rete non si intende la mera connettività, ma la capacità di interoperare attraverso sistemi di controllo distribuito o di frontiera (edge computing). In altre parole i sistemi meccatronici che si trovano sul bordo (sensori, sistemi di visione, processori) generano dati che sono diversi, variegati, possono essere sani o deteriorati, ed è necessario effettuare su di essi alcune operazioni. Diventa sempre più consolidata l’idea che questa fase venga fatta direttamente sulla periferia, sul macchinario o sul sensore, che dotato di capacità di calcolo può essere parte attiva del processo di raccolta ma anche di controllo. L’idea per ridurre questi problemi è quella di decentralizzare alcuni calcoli e alcune analisi (gestione allarmi, pulizia dei dati e così via) a livello locale (edge) o nei sistemi intermedi che costituiscono il punto di connessione con il cloud. I sistemi digitronici diventano quindi parte attiva di questo processo e non solo generatori passivi di dati. Il ruolo principale di di questa architettura è quello di abilitare il controllo distribuito, cioè la possibilità di non avere più un decisore centralizzato per tutte le azioni che devono essere fatte, ma permettere che la maggior parte delle funzioni avvengano a livello di singolo dispositivo.
Ma la digitronica sarà molto di più: sarà innovazione e cambiamento tecnologico insieme alla integrazione nei processi aziendali con risvolti di tipo sociale, in quanto cambierà il modo di legare consumatori e aziende, ma anche dipendenti e imprese. Non ci sono solo dati di processo a essere raccolti ma anche dati su come l’operatore interagisce con il macchinario. La realtà aumentata integrata con i sistemi automatici permetterà agli operatori di avere istruzioni e informazioni in tempo reale, cosi come la robotica collaborativa, integrata con i sistemi meccatronici permetterà al lavoratore di avere dei supporti per svolgere compiti onerosi e ripetitivi, cambiando anche il modo in cui si può lavorare. E non si parla solo dei lavoratori, anche i clienti finali potranno interagire con il prodotto meccatronico per fornire al produttore informazioni utili sul suo modo di uso. La digitronica offre l’occasione per una interazione sempre più complessa con tutti gli attori del processo.
a cura di Loris Cantarelli
Condividi l'articolo
Scegli su quale Social Network vuoi condividere