Quando si tratta di ispezione ottica 3D dei processi produttivi in impianti a colata continua, in laminatoi a caldo e per tubi, è normale…
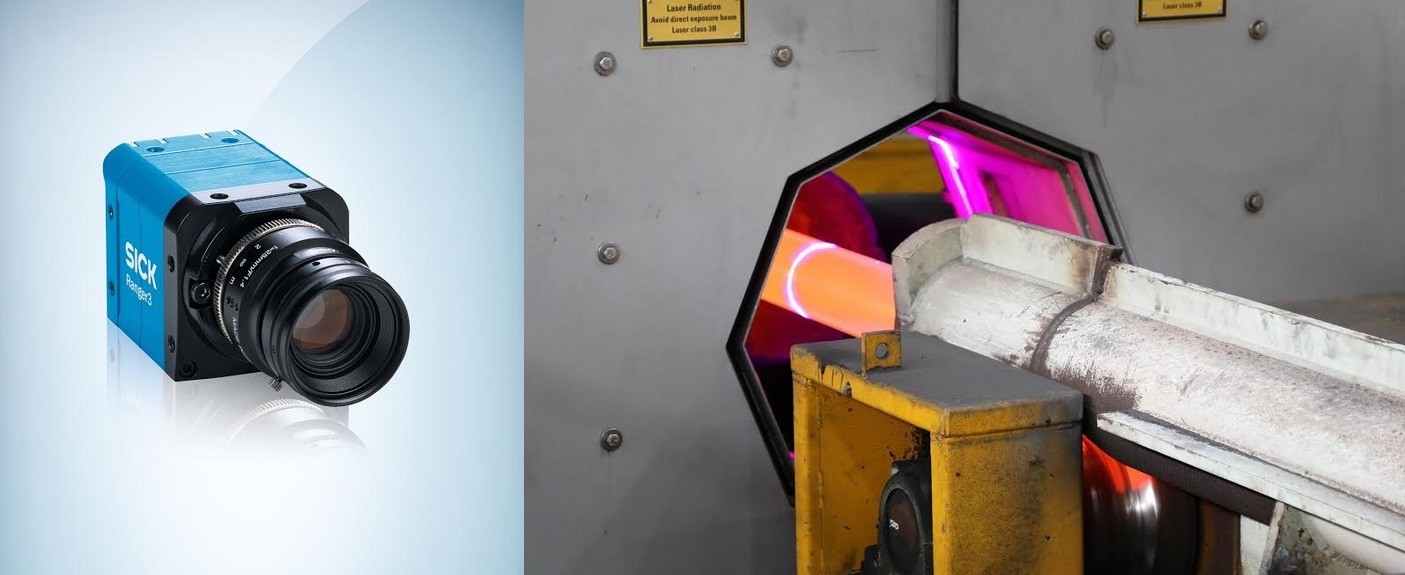
Quando si tratta di ispezione ottica 3D dei processi produttivi in impianti a colata continua, in laminatoi a caldo e per tubi, è normale avere a che fare con superfici incandescenti, calore, sporco e umidità.
Esattamente come avviene in IMS Messsysteme GmbH, ai vertici nel settore dell’acciaio. Per andare risolvere le difficoltà derivanti dall’ambiente lavorativo, da oltre un anno, l’azienda impiega sistemi di visione 3D, ed in particolare la camera streaming Ranger3 di Sick, che ha migliorato sensibilmente i sistemi di ispezione costruiti da IMS e, al contempo, ha aperto nuovi campi applicativi e opportunità commerciali.
IMS Messsysteme GmbH sviluppa e produce sistemi di misurazione isotopici, a raggi infrarossi e ottici per l’impiego industriale nel settore dell’acciaio e del materiale non ferroso. L’azienda, fondata nel 1980, dopo 40 anni impiega circa 450 dipendenti dislocati in tutto il mondo. «Con soluzioni complete, come il sistema di misurazione X-3Dvision, ci siamo conquistati la posizione di leader tecnologici e di mercato per impianti a colata continua, laminatoi a caldo e per tubi», afferma Zvezdan Pejovic, product e sales manager per sistemi di ispezione 3D ottici presso IMS.
I sistemi possono ispezionare i profili del materiale prodotto durante il processo di lavoro e alle condizioni più estreme, verificando in un’unica stazione dimensioni, contorno e linearità nonché errori superficiali come fessure, accumuli, inserimenti di materiali o cavità. «Più facilmente si riconoscono gli errori, più velocemente è possibile correggere i processi di lavorazione ed evitare scarti», prosegue Pejovic. «Ecco perché i nostri sistemi di misura vengono usati già in fase di produzione a caldo. Qui i profili e i tubi raggiungono ancora una temperatura attorno ai 1000 °C, pertanto è necessario che il sistema di misura abbia caratteristiche tecniche e meccaniche adatte a resistere in un ambiente così difficile».
I sistemi di misura X-3Dvision di IMS vengono usati per un’ispezione a 360° di prodotti con caratteristiche geometriche diverse. «Per poter rilevare l’intera superficie di profili o tubi senza occlusioni, integriamo più camere e illuminatori laser in una configurazione circolare, in cui il profilo viene ispezionato mentre attraversa il sistema di misura», spiega Pejovic la configurazione del portale. «I componenti del sistema di misura vengono integrati nel robusto telaio e qui sono protetti dal contatto diretto con l’ambiente circostante. Al fine di garantire temperature ambiente stabili, le camere e i laser vengono raffreddati ad aria e acqua, di modo che i risultati della misurazione siano precisi e riproducibili».
La precisione è anche uno dei punti di forza dei sistemi di misurazione di IMS: per misurare i profili, l’azienda offre una risoluzione tipica di 0,05 mm e una riproducibilità di ±0,08 mm; nell’ambito dell’ispezione superficiale vengono misurati e riconosciuti affidabilmente solchi, fessure e graffi fino a una larghezza di 0,03 mm, una lunghezza di 10 mm e una profondità di 0,3 mm (dati di esempio relativi ad un’installazione esistente a valle di un laminatoio riduttore per tubi, con riferimento a una velocità di produzione di 10 m/s).
In base al tipo e alla forma del profilo, nei sistemi di misura di IMS vengono usate da 3 a 8 camere per un’ispezione a tutto tondo. «In uno dei nostri ultimi impianti abbiamo tuttavia integrato un numero maggiore di sensori di visione in 3D, arrivando fino a 22 Ranger3», continua Pejovic. «In questo modo siamo riusciti a soddisfare la richiesta di un cliente che voleva un sistema di misura e ispezione unico, altamente preciso, per la sua intera gamma di profili H, L, C e CZ».
Per estrarre i dati 3D direttamente a bordo della camera, Sick ha sviluppato la tecnologia ROCC. Il sensore CMOS del Ranger3 ricostruisce in modo preciso il profilo 3D dell’oggetto a partire dall’immagine registrata dalla lama laser. Ciò vuol dire che la videocamera, senza alcuna onerosa rielaborazione, mette a disposizione coordinate 3D pronte per il sistema di misura X-3Division di IMS. Contemporaneamente, l’interfaccia Gigabit Ethernet garantisce alla camera streaming una trasmissione in tempo reale anche di grandi quantità di dati misurati. «A seconda dell’applicazione, le camere acquisiscono fino a 24 mila profili al secondo e ciò corrisponde a una media dati di tutte le camere fino a 4 Gbit/s», conferma Pejovic. «Con le camere Ranger3 di Sick, siamo riusciti a trasformare il nostro X-3Dvision in un sistema in linea per l’ispezione multiprofilo. In questo modo è in grado di raggiungere una precisione elevatissima anche in caso di velocità impegnative. Al contempo, può inviare in modo tempestivo una notifica relativa anche al più piccolo scostamento, in modo da consentire una correzione del processo durante colata e laminazione».
Resta comunque la domanda sul perché, per prodotti così grandi e robusti come profili e tubi in acciaio, ferro o alluminio, sia necessario l’aiuto di sensori 3D ad alta risoluzione per riconoscere in sicurezza anche i più piccoli scostamenti ed errori. «Da una parte per noi si tratta di una questione di principio”, dice Zvezdan Pejovic. “In qualità di leader di mercato, ci impegniamo a fornire ai nostri clienti sistemi di misura precisi, affidabili e robusti, affinché essi, con i loro prodotti, siano competitivi sul mercato mondiale. Gli altri aspetti sono di natura pratica ed economica. Infatti, misurazioni e dimensioni errate potrebbero causare reclami e rifiuti da parte delle aziende che si occupano dell’ulteriore elaborazione. Inoltre, se questi pezzi difettosi dovessero proseguire nel processo senza essere individuati, sussisterebbe il pericolo di danneggiare gli utensili nel corso della lavorazione. D’altra parte, durante la produzione di solito è possibile riconoscere eventuali danni agli utensili e la produzione può essere arrestata, al fine di evitare inutili scarti. Nel caso della produzione di tubi, invece, gli errori verrebbero rilevati solamente dopo ore, se non giorni, durante il processo finale di lavorazione, e questo causerebbe la ripetizione completa del processo di produzione, con un danno economico elevato. A seconda dell’ulteriore utilizzo, anche piccole fessure, cavità oppure inclusioni di materiali possono compromettere la qualità e l’impiego del prodotto finale».
Con l’aiuto della camera streaming Ranger3, IMS garantisce non solo un’elevata qualità del processo produttivo e dei prodotti realizzati, ma per l’azienda si aprono anche nuove opportunità di mercato. «Le alte velocità di misurazione e trasmissione dei sensori di visione 3D di Sick rendono utilizzabili i nostri sistemi di ispezione in tutti quei nuovi campi di applicazione caratterizzati da elevate velocità di processo», conclude Pejovic. «Per esempio, nella produzione di binari e ancora di più nella produzione di materiali ad asta oppure di fili laminati con velocità di avanzamento fino a 100 m/s».
a cura di Loris Cantarelli
Condividi l'articolo
Scegli su quale Social Network vuoi condividere