Luciano Massone spiega perché il World Class Manufacturing è così importante per FCA e perché non è sufficiente investire nel digitale per essere efficienti.
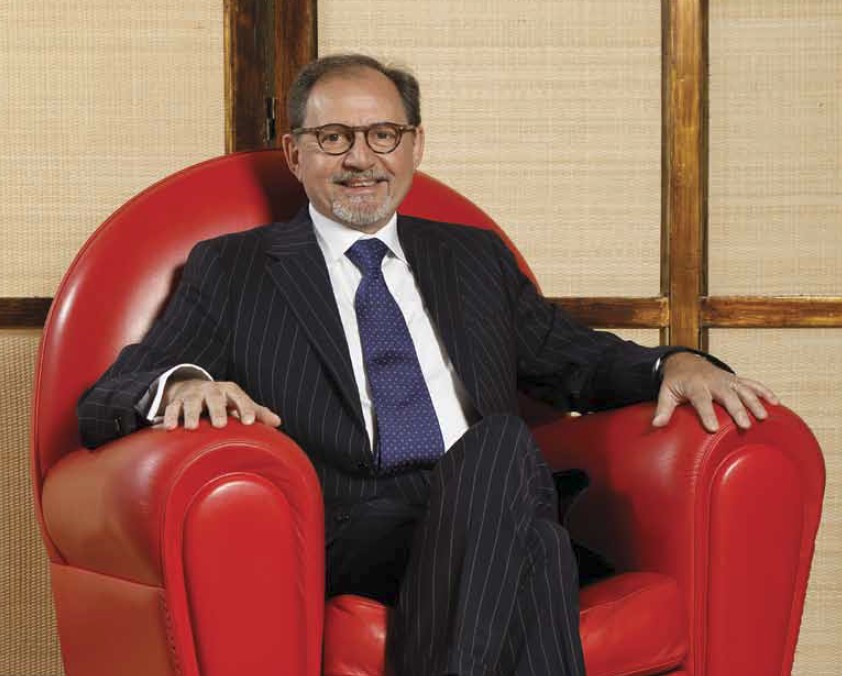
Abbiamo incontrato Luciano Massone per capire perché il World Class Manufacturing è così importante nell’universo produttivo FCA e non è sufficiente investire nel digitale per essere efficienti.
Incontrare Luciano Massone vuol dire avere l’opportunità di confrontarsi con chi ha implementato il World Class Manufacturing nell’universo Fiat, contribuendo a cambiare volto al modo di produrre del grande Gruppo industriale italiano. Nella sua lunga carriera Massone ha potuto quindi approfondire il tema del miglioramento continuo in fabbrica e della ricerca dell’efficienza produttiva sfruttando tutte le opportunità legate all’innovazione tecnologica e non solo.
Proprio per questi motivi lo abbiamo incontrato e abbiamo parlato del suo percorso professionale, di come stanno cambiando le fabbriche italiane e delle opportunità e dei rischi legati alla digitalizzazione dei processi produttivi.
Nella sua carriera si è occupato di sviluppare e diffondere il WCM (World Class Manufacturing) nell’universo produttivo FCA: quali difficoltà avete incontrato lungo questo percorso? C’è stato un momento in cui avete capito di essere sulla giusta strada?
Il World Class Manufacturing porta una nuova filosofia di lavoro, un approccio al miglioramento continuo che gradualmente pervade tutti i livelli dell’organizzazione produttiva. Per avviare un cambiamento di questo tipo, le difficoltà non sono poche. All’inizio, la spinta deve partire dall’alto. È necessario “conquistarsi” il commitment dei Top Manager. E questo si fa dimostrando benchmark, esempi di buone applicazioni che possono essere replicate e poi… mantenendo le promesse. Allo stesso modo, bisogna dare risposte a chi lavora, dimostrando di riuscire a cambiare davvero le condizioni di lavoro, anche e soprattutto raccogliendo la propositività che è latente in tutti. Queste sono le vere sfide, soprattutto all’inizio.
Una volta cominciato poi è una “Never Ending Story”, un continuo guardarsi dentro per trovare opportunità di miglioramento. Sicuramente l’evidenza dei risultati raggiunti (in termini di ergonomia del posto di lavoro, produttività, riduzione di breakdown e miglioramento degli indicatori di qualità), dà fiducia e crea energie per rinnovare gli sforzi e alimentare quel volano che alla fine diventa motore per il cambiamento.
Oggi il WCM come sta cambiando? Quali sono le sfide più importanti per rendere una fabbrica efficiente?
Il metodo evolve continuamente. Non si tratta di una rivoluzione ma di un continuo adeguamento, che è necessario da un lato per raffinare approcci e strumenti, dall’altro per tener conto dei nuovi stimoli che arrivano dall’evoluzione tecnologica come per esempio le opportunità che si possono generare per via di una corretta digitalizzazione dei processi. Questa si può considerare una delle sfide più interessanti del momento.
In un recente convegno l’ho sentita definire il WCM come “una bussola per evitare la digitalizzazione degli sprechi”. Può spiegarci meglio che cosa intendeva?
La digitalizzazione dei processi può essere una grande opportunità, da un lato per individuare nuove perdite e sprechi, dall’altro per poterli attaccare in maniera efficace ed efficiente. Il rischio che vedo è quello di innamorarsi di alcune soluzioni “smart” e quindi perder di vista i processi e i veri bisogni della fabbrica, “coprendoli” con soluzioni software che in alcuni casi possono anche inibire il processo di miglioramento continuo. Il WCM in questo senso basa la sua azione sull’individuazione (prima) e la risoluzione (dopo) di perdite e sprechi, quindi aiuta a rimanere attaccato ai problemi e ai veri benefici per la fabbrica. Da qui si analizzano soluzioni, anche “digital”, che garantiscano comunque la flessibilità dei processi e l’autonomia nello sviluppo.
Il fenomeno della digitalizzazione è peraltro già insito nella logica del WCM in tutti i pilastri prima ancora che si parlasse di Industria 4.0. Per fare un esempio su tutti, parliamo di Cost Deployment (CD). Durante il percorso implementativo del CD in azienda all’inizio s’impara e ci si allena a riconoscere perdite e sprechi, che sono dapprima stimati e poi via via calcolati in maniera sempre più precisa e puntuale sulla base di dati reali. Oggi la sistematizzazione della raccolta dati per questi calcoli richiede strumenti digitali che permettono una collezione efficiente, sicura e in molti casi in real time. Si chiama CD digitale ed è presente in azienda negli stabilimenti più avanzati da parecchi anni.
Per alcuni analisti l’Industria 4.0 potrebbe essere in grado di rilanciare la competitività del sistema industriale italiano. Lei cosa ne pensa? Siamo davvero di fronte a un momento decisivo per il futuro del manifatturiero nel nostro Paese?
Sicuramente il momento è molto fertile e le opportunità che offrono le nuove tecnologie sono tante e molto interessanti. Sotto il cappello di Industria 4.0 si nascondono però molti approcci diversi. Molti settori, come per esempio il banking, hanno saputo già approfittare di queste opportunità, in molti casi cambiando i paradigmi del business, conquistando quindi terreno e vantaggio competitivo. La manifattura, a mio avviso, è in una fase esplorativa e, fatta eccezione per alcuni buoni esempi, non vedo ancora evidenza di una vera e propria rivoluzione digitale in atto. Non vi è dubbio però che le opportunità esistono e vanno investigate e colte; possono segnare una svolta, ma siamo solo all’inizio.
Se da un lato il WCM fornisce un paradigma metodologico per aiutarci a non fare passi falsi nell’implementazione, dall’altro è necessario affrontare il cambiamento a 360 gradi, non solo tecnologico. Un approccio serio sullo sviluppo delle persone e change management è obbligatorio. Dovremo rivedere i ruoli e le competenze delle persone in fabbrica, rivedere le loro attività, accompagnarle in un cambio di mindset richiesto in questo tipo di cambiamenti. Anche in questo senso i pilastri manageriali del WCM aiutano e favoriscono questo processo.
La fabbrica sta cambiando volto diventando sempre più intelligente e digitale. In questo contesto come deve cambiare la macchina utensile per rispondere alle nuove esigenze e ai nuovi paradigmi produttivi?
Le macchine devono evolvere come i telefoni sono evoluti verso gli smartphone. Ogni euro d’investimento in tecnologia deve aprire opportunità per l’azienda e per le persone. Flessibilità tecnologica e organizzativa, che vuol dire anche semplice composizione e scomposizione del layout e set-up veloci. Manutenzione facile e sempre più predittiva. Autodiagnosi dei problemi. Dialogo autonomo e integrazione tra impianti. Questi sono solo alcuni dei concetti che devono guidare la progettazione dei nuovi impianti, che permetteranno quindi di lasciare sempre più spazio alla creatività e all’intelligenza dell’individuo, aumentando il valore per tutti gli stakeholders.
Digitalizzare e virtualizzare la fabbrica sembra oggi uno sviluppo quasi obbligato per un grande player industriale. Secondo lei, anche piccole realtà andranno in questa direzione o si tratta di elementi d’innovazione produttiva che rimarranno confinati nelle grandi aziende?
Questo è un punto chiave. Oggi può esserci un problema di accessibilità di certe soluzioni per la piccola e media impresa, che costituisce il grosso del tessuto produttivo italiano. Se da un lato il prezzo di alcune soluzioni specifiche si sta abbassando quello che ancora manca è una visione integrata delle soluzioni e competenze adeguate per poterne sfruttare a pieno i benefici. Manca ancora una visione di sistema. È probabile che le grandi imprese saranno i primi player di questa rivoluzione, ma a medio termine l’intera catena del valore verrà coinvolta e “trascinata” in questa trasformazione e ne beneficerà.
In una fabbrica che sta cambiando così radicalmente in che direzione si deve evolvere il ruolo dell’uomo? Quali nuove competenze sono richieste a chi lavora in uno stabilimento FCA oggi?
L’uomo mantiene un ruolo fondamentale. Rimane il driver del cambiamento. Creare sistemi super-efficienti ma ingessati è potenzialmente un errore. I sistemi devono poter evolvere, rimanere aperti, facilmente riconfigurabili. Devono quindi permettere autonomia nel miglioramento continuo. In questo senso quindi servono le capacità di governo di questi sistemi unite a capacità di gestione dei processi. L’esperienza del singolo rimane fondamentale e si deve fondere con il know-how progettuale e la competenza tecnologica.
La parola “innovazione” viene spesso indicata come la chiave del successo di un’azienda. Per lei cosa vuol dire fare innovazione in azienda?
Vuol dire sapere individuare i propri limiti e trovare soluzioni per superarli. L’innovazione deve servire per eliminare i compromessi e trovare soluzioni “win-win”, in cui tutti vincono. Per fare questo oggi l’innovazione verticale che ha caratterizzato il recente passato non è più vincente. Infatti è più lenta, e non raggiunge gli stessi risultati. Il paradigma per cui la R&D pensa, l’ingegneria sviluppa soluzioni e la produzione esegue ormai è superato. Questi mondi si devono integrare, devono alimentarsi reciprocamente e rinnovarsi in continuo e in parallelo. Oggi tutto è più vicino: le possibilità offerte dalla globalizzazione e dalle nuove tecnologie aprono infinite possibilità. Sta a noi scoprirle.
Quali sono a suo avviso gli elementi più urgenti su cui intervenire per rimettere l’industria italiana nella condizione di crescere?
Bisogna cominciare dalle persone. Far crescere le competenze su temi nuovi, non farci trovare impreparati. Dobbiamo andare a imparare dalle eccellenze mondiali e cominciare a costruirci la nostra “strategia Industria 4.0” a partire dalle università e dai centri di ricerca. L’infrastruttura tecnologica a supporto viene subito dopo ma è fondamentale. Anche un’azienda grande ha bisogno di un’infrastruttura e un impianto normativo a livello Paese, incluso un adeguato livello di cyber-security che abiliti e favorisca il cambiamento senza alimentare paure e fungere da blocco e/o da freno.
Secondo lei, come sarà uno stabilimento automotive fra vent’anni?
Uno stabilimento senza confini, dove non saranno così evidenti i limiti tra produzione e logistica, tra qualità e manutenzione; un vero sistema produttivo integrato, vicino alle esigenze del cliente e che sia un elemento di competitività per l’azienda tutta. Uno stabilimento dove convivranno e s’integreranno competenze diverse, tecnologiche, di progettazione digitale, di governo di sistema e che sia continua sorgente d’idee e nuovi brevetti. Un luogo dove sarà facile e automatico raccogliere, condividere e analizzare dati in grandi quantità ad alta velocità e a basso costo.
Uno stabilimento dove la realtà virtuale diventerà un supporto quotidiano per anticipare i problemi e simulare scenari di flessibilità. Uno stabilimento dove la tecnologia sia al servizio dell’uomo e non la sua sostituzione. Viviamo in un tempo di forte cambiamento e quindi di grandi opportunità che, non nego, mi stimolano molto e per certi versi gioisco pensando ai giovani che, se preparati a questo tempo, potranno diventarne i protagonisti ed essere in grado di dar forma al futuro che ci aspetta.
Chi è Luciano Massone
Luciano Massone ricopre dal 2014 il ruolo di Head of World Class Manufacturing EMEA & WCM Development Center. Nel 2015 in aggiunta ai suoi precedenti incarichi gli viene affidato il ruolo di coordinatore dei World Class Projects a livello global per il Gruppo FCA. Abruzzese di origine, entra in FIAT, stabilimento Sevel nel 1981 in qualità di Manpower Manager, ricoprendo incarichi di crescente responsabilità inizialmente nell’area Manufacturing, poi nell’area Relazioni industriali e Gestione del personale, dapprima negli stabilimenti e successivamente negli enti centrali di FIAT Auto. Nel 2005 a seguito di un’esperienza in Giappone e negli USA è il pioniere dell’odierno WCM, allora FAPS (Fiat Auto Production System),veicolando e implementando il metodo WCM prima in Fiat e successivamente in CNH Ind. e Chrysler. La struttura del Development Center da lui gestita è centralizzata per tutto il Gruppo FCA, dove la metodologia WCM viene implementata a livello globale, e comprende la Business Unit Training and Consulting, il programma per Suppliers, il Dipartimento Manufacturing Innovation nonché il coordinamento del sistema di Audit. Luciano Massone è sposato e ha due figli.
a cura di Maria Bonaria Mereu
Condividi l'articolo
Scegli su quale Social Network vuoi condividere