Dai principi Lean alla digitalizzazione, lo stabilimento Acque Minerali San Benedetto a Scorzè dimostra come nella fabbrica del futuro il cambiamento coinvolga il prodotto, il processo ma anche la cultura degli operatori
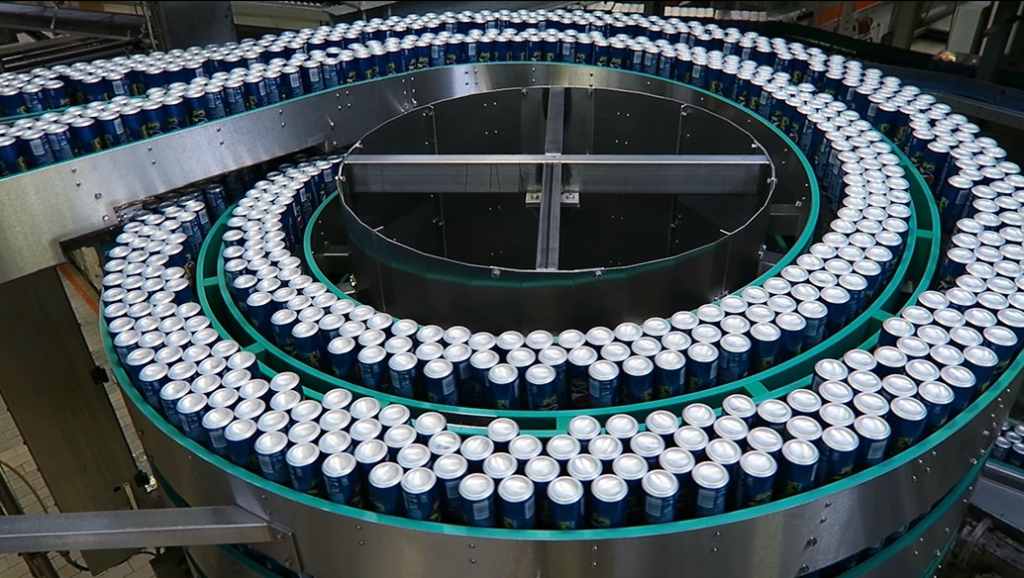
Dai principi Lean alla digitalizzazione, lo stabilimento Acque Minerali San Benedetto a Scorzè dimostra come nella fabbrica del futuro il cambiamento coinvolga il prodotto, il processo ma anche la cultura degli operatori
“Innovazione vuol dire cercare di fare qualcosa che gli altri non fanno, lavorando non obbligatoriamente con la tecnologia più recente ma anche usando l’esistente. Il tutto cercando di spendere meno e mantenendo elevata l’efficienza produttiva”. Così l’ing. Rosario De Marchi, direttore dello stabilimento di Scorzè (VE) di Acque Minerali San Benedetto, spiega la sua, solo apparentemente semplice, ricetta per fare innovazione. “Oggi – prosegue De Marchi – dobbiamo essere consapevoli che il cliente sta cambiando e questo vale non solo per il beverage, ma per tutti i settori. Il mercato chiede prodotti sempre nuovi e tempi di attraversamenti ridotti, quindi o ti attrezzi oppure qualche tuo concorrente lo farà prima di te. Un’azienda deve essere pronta a fare innovazione di prodotto, di processo e di cultura: questi tre aspetti non possono più essere separati”.
Digitalizzare per avvicinare
Questo approccio è alla base anche dell’importante processo di digitalizzazione delle linee produttive realizzato nello stabilimento di Scorzè. Ad innescare questa evoluzione è stata infatti la volontà di sensibilizzare tutto il personale (dalla manutenzione al capo impianto, passando per l’operatore di linea) rispetto al tema dell’efficienza produttiva o, per essere più precisi, di quello che viene identificato come “efficienza totale di un impianto (OEE)”. Con questa espressione si definisce un indicatore percentuale che rappresenta il rendimento globale di una risorsa produttiva durante il tempo nel quale questa è disponibile a produrre. “L’OEE – spiega De Marchi – è per noi un indicatore fondamentale e volevamo che questo dato fosse visibile in real-time da tutti gli operatori in modo da sottolinearne l’importanza e il valore. Per riuscire a portare questo dato a bordo linea abbiamo quindi digitalizzato la produzione, cioè dotato ogni linea di un computer dove attraverso il sistema ILIS (informatizzazione linee imbottigliamento Scorzè) fosse mostrato il grado di efficienza della linea aggiornato ogni 15 minuti”.
Importante sottolineare come tutto il sistema ILIS sia stato sviluppato internamente. “È un progetto nato come software per analizzare i fermi produzione che si è poi evoluto con altre funzioni. ILIS sta crescendo, per esempio in futuro puntiamo a estrarre i dati di efficienza non solo per una singola linea, ma anche per codice prodotto. In questo modo potremo quindi capire quando è più efficiente produrre un determinato prodotto in una determinata linea e quando invece fare scelte diverse”
Raggiunto il primo obiettivo, “portare” l’OEE in produzione e metterlo a patrimonio comune, a Scorzè si è lavorato per introdurre il concetto di automanutenzione predittiva, mostrandone i vantaggi proprio sull’OEE. “Volevamo che l’operatore capisse i benefici di attività come l’ingrassaggio e la lubrificazione che, possono sembrare banali, ma hanno un importante impatto sull’efficienza complessiva e, di conseguenza, sul valore del nostro prodotto”. L’automanutenzione, cioè le operazioni di manutenzione eseguite direttamente dall’operatore, sono fondamentali secondo De Marchi per mantenere elevata l’efficienza dell’impianto. “Qui a Scorzè – prosegue il direttore dello stabilimento veneziano di Acque Minerali San Benedetto – fermiamo le linee ogni settimana per 3-4 ore per completare le attività di manutenzione predittiva. La scelta di eseguire questa attività durante l’orario di lavoro, e non il sabato pomeriggio a produzione ferma come succedeva anni fa, è motivata dalla volontà di coinvolgere tutti gli operatori in modo da formarli e da spiegargli il valore di fare manutenzione sulla macchina”. Sempre con l’obiettivo di dotare tutti gli operatori di competenze tecniche di base, in Acque Minerali San Benedetto è previsto che tutti gli operatori della produzione passino un periodo, solitamente durante la “bassa stagione”, impegnati in affiancamenti in manutenzione.” In questo modo l’operatore impegnato in produzione ha le competenze necessarie sia per fare l’automanutenzione sia per una prima diagnosi, aiutando così il manutentore al momento dell’intervento e riducendo i tempi di ripristino”.
Proprio i manutentori sono stati coinvolti nella fase successiva di diffusione di ILIS. “Nel tempo abbiamo capito come la comunicazione via telefono tra produzione e manutenzione non era sempre efficace. Abbiamo quindi dotato tutti i manutentori di un tablet che permettesse loro di accedere in tempi reale ad ILIS e avere quindi una panoramica sull’andamento delle linee”. Questa semplice implementazione, via tablet ILIS mostra prestazioni ed OEE delle linee e, in caso di guasto, quale macchina stia rallentando la linea, ha portato diversi benefici: primo fra tutti una maggiore efficacia degli interventi di manutenzione. “Il manutentore conoscendo lo stato delle linee è in grado spesso di determinare la gravità di una microfermata, valutarne l’urgenza e ottimizzare così le sue attività durante il turno. Per i responsabili della manutenzione inoltre in questo modo diventa più semplice gestire al meglio le proprie risorse”. Evidente come le potenzialità di ILIS siano molte e, in piena coerenza con le tendenze dell’Industry 4.0, si stia valutando di ampliare il range di valori rilevati e monitorati dal dispositivo. “Stiamo introducendo su progetti piloti, che potenzialmente potremo poi integrare in ILIS, la possibilità di misurare anche altri parametri: dalle temperature all’assorbimento dei motori delle linee, fino ai tempi richiesti per raggiungere determinate temperature. In questo modo non solo diamo più strumenti al manutentore per essere più rapido ed efficace nel suo intervento, ma puntiamo a riuscire a capire quando bloccare una linea prima che si verifichi un blocco o un deterioramento della qualità della produzione. Questa attività ha un impatto economico non banale, si tratta infatti di installare e mettere in rete molti sensori, ma gradualmente e senza rallentare la produzione la stiamo portando avanti”.
Evoluzione a 360°
Con 23 linee attive, lo stabilimento di Scorzè di Acque Minerali San Benedetto conta su un parco macchine installato cospicuo costituito anche da macchinari non certo nuovissimi. Il direttore di stabilimento De Marchi conferma però come la vetustità di alcune macchine non sia stato un freno al processo di digitalizzazione. “Ovviamente sulle macchine nuove questa attività è più semplice, ma il lavoro tecnico e progettuale necessario ad implementare questi dispositivi anche su macchine già installate fa crescere il patrimonio di competenze tecnologiche interne all’aziende. Inoltre, gestendo internamente questo processo riusciamo anche a coinvolgere maggiormente i nostri tecnici sull’importanza e l’impatto di questo processo di efficientemento”.
Come abbiamo già anticipato Acque Minerali San Benedetto è da sempre pioniere sia nel realizzare innovazione internamente sia nello sfidare i fornitori a cercare di innovare e di innovarsi. “Bisogna tenere presente che lo stabilimento di Scorzè ha una capacità produttiva giornaliera intorno ai 12 milioni di bottiglie, inoltre queste linee sono impegnate in processo ad alta velocità ed energivoro. Questa mole di prodotti, tra l’altro composta da un panel ampissimo di formati diversi, non consente inefficienze e ritardi in produzione, altrimenti la logistica sarebbe messa in crisi. Il processo di imbottigliamento deve essere quindi efficiente, puntuale e in grado di gestire cambi di formato frequenti, altrimenti si generano sprechi e costi che il mercato non è più disposto a pagare”.
Indossando i muda glasses
Il focus sull’OEE è, come abbiamo visto, alla base del processo di digitalizzazione delle linee e della nascita del progetto ILIS, ma è anche parte di un processo più ampio di implementazione dei principi Lean nello stabilimento. “Abbiamo iniziato nel 2012 – racconta De Marchi -, ma per i primi due anni abbiamo realizzato solo progetti pilota ma che, comunque, hanno portato dei benefici. Successivamente abbiamo cominciato a lavorare su questi temi in modo più significativo cercando di trasmettere questi concetti a tutti i dipendenti dello stabilimento”. Per De Marchi alla base di un’efficace implementazione della Lean Manfacturing c’è un cambiamento radicale e culturale delle persone che, solo dopo aver compreso e fatti propri i fondamenti Kaizen (i concetti base della filosofia Lean NdR), possono innescare il cambiamento all’interno dell’azienda. “L’obiettivo è che ogni persona guardi il proprio lavoro indossando degli immaginari muda glasses (letteralmente degli “occhiali per vedere gli sprechi”) in modo da capire quali siano le operazioni che hanno un valore per il nostro cliente e quali siano invece sprechi. Si tratta di un’importante evoluzione culturale che abbiamo iniziato organizzando giornate formative fuori azienda, che hanno visto circa 350 persone coinvolte, utili a raccontare il motivo di questo cambiamento”. Il passo successivo è stato iniziare la fase applicativa dei concetti Lean individuando in azienda persone dedicate a vari temi e promuovendo la creazione di gruppi di lavoro per la stesura e la raccolta di proposte di interventi di efficientemento. “Abbiamo raccolto circa 3mila proposte di ogni tipo e complessità, ne abbiamo valutato la fattibilità e di ciascuna abbiamo spiegato, tramite schermi installati nello stabilimento, se approvata come sta procedendo la sua implementazione oppure se rifiutata i motivi della nostra scelta. L’obiettivo è coinvolgere le persone che lavorano nello stabilimento e, per farlo, sono convinto si debba spiegare cosa stiamo facendo e cosa faremo in futuro”. Ovviamente il processo di implementazione Lean è ancora in corso e, nell’ultimo anno, ha coinvolto in particolare le attività di manutenzione. “Abbiamo creato una nuova funzione, l’ingegneria di manutenzione, che raggruppa diversi specialisti per portare avanti le metodologie Lean in parallelo alla standardizzazione delle attività di manutenzione. Oltre all’attività di automanutenzione delle linee, stiamo anche introducendo elementi di manutenzione predittiva, tra cui l’ispezione termografica delle linee, in modo da programmare le attività di riparazione delle macchine (come ad esempio la sostituzione di un componente) senza impatti sull’efficienza della produzione”. L’evoluzione Lean ha coinvolto anche i principali fornitori di Acque Minerali San Benedetto anche se, come ci confida De Marchi, non è stato semplice far comprendere i vantaggi derivanti dall’applicazione di questi principi produttivi.
Un futuro senza sprechi
Il processo di innovazione è continuo e i primi analisti cominciano ad immaginare quale sarà il volto della manifattura dopo che la cosiddetta “quarta rivoluzione industriale” sarà completata. “Dobbiamo ancora attrezzarci bene per il 4.0…– risponde sorridendo De Marchi –, nel senso che nel manifatturiero italiano si deve realizzare la sinergia completa tra IT e produzione, due ambiti che non possono più essere divisi. Credo che questo sia uno dei punti chiave: dopo l’integrazione tra manutenzione e produzione, oggi bisogna mettere in relazione le funzioni informatiche con quelle produttive. Se invece proviamo a guardare ancora più in là, mi immagino in un futuro una fabbrica dove non ci siano più scarti e che finalmente sia a spreco zero. Per arrivarci c’è però tanto da fare, sia a livello tecnologico sia di organizzazione aziendale”.
Quale tecnologia per la fabbrica intelligente?
L’evoluzione dello stabilimento di Scorzè ha ovviamente influenzato il rapporto con i fornitori di macchine industriali a cui oggi Acque Minerali San Benedetto esprime richieste molto chiare. “Quando acquistiamo una macchina – spiega l’ing. De Marchi – richiediamo al costruttore di fornire un’interfaccia che aiuti l’operatore nella gestione degli allarmi e dei primi interventi di riparazione, ma anche che i costruttori si allineino al processo di standardizzazione della componentistica che stiamo portando avanti con l’obiettivo di velocizzare il lavoro del manutentore. Sempre in ottica di manutenzione chiediamo ai nostri fornitori di organizzare pacchetti formativi per gli operatori e corsi più approfonditi con i nostri manutentori”. Oltre ad acquistare tecnologia da fornitori esterni, Acque Minerali San Benedetto realizza internamente parte delle macchine e delle soluzioni utilizzate in produzione e, per la progettazione di queste nuove macchine, i dati raccolti in produzione sono utilissimi. “Inseriamo all’interno del nostro PLM tutti i dati che raccogliamo creando così un database di informazioni che è poi consultato dai colleghi della divisione Engineering interna per realizzare nuove soluzioni sempre più efficienti e performanti. Vogliamo infatti valorizzare il patrimonio di know how interno ed è anche per questo motivo che in Acque Minerali San Benedetto l’ideazione e la realizzazione di molti progetti viene affidata a personale interno”.
Un colosso da 12 milioni di bottiglie al giorno
Lo stabilimento di Scorzè è la prima sede di Acque Minerali San Benedetto e, ancora oggi, è il principale sito produttivo del Gruppo a cui si affiancano Popoli (Pescara), Donato (Biella), Nepi (Viterbo), Viggianello (Potenza), Atella (Potenza) e altri due di proprietà in Spagna, uno in Polonia, uno in Ungheria e stabilimenti in Joint Venture in Messico e Repubblica Dominicana.
A Scorzè oggi si imbottiglia tutta la gamma di bevande del Gruppo: dalle bottiglie in PET, che vengono realizzate internamente partendo al granulo, al vetro fino alla lattina, arrivando a una produzione di circa 12 milioni di bottiglie al giorno. Inoltre recentemente è stata aggiunta la produzione di té in buste.
Per inquadrare le dimensioni industriali è utile ricordare che Acque Minerali San Benedetto è una Total Beverage Company completamente italiana con un fatturato consolidato di 730 milioni di euro, 1.800 dipendenti nel mondo e 44 linee di imbottigliamento in Italia che possono produrre sino a 19 milioni di bottiglie al giorno.
a cura di Maria Bonaria Mereu
Condividi l'articolo
Scegli su quale Social Network vuoi condividere