Sfruttare nuove metodologie produttive e coinvolgere tutti i reparti della produzione sono le leve che hanno reso l’AGAP di Maserati uno stabilimento all’avanguardia.
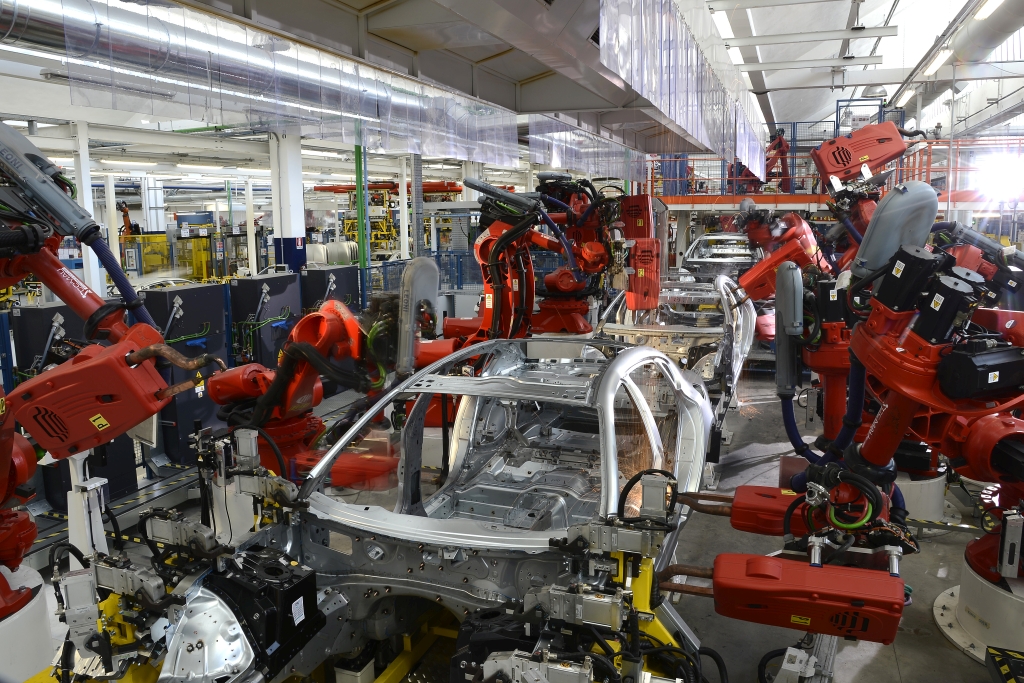
Sfruttare nuove metodologie produttive e coinvolgere tutti i reparti della produzione sono le leve che hanno reso l’AGAP di Maserati uno stabilimento all’avanguardia.
La fontana del Nettuno è uno dei simboli più rappresentativi della città di Bologna. L’opera fu progettata nel 1563 dall’architetto Tommaso Laureti, mentre l’imponente statua in bronzo che la sormonta venne realizzata dallo scultore fiammingo Jean de Boulogne, detto Giambologna. Il “Gigante” (così i bolognesi hanno ribattezzato la statua) è una rappresentazione del dio Nettuno, che domina dall’alto lo scorrere delle acque impugnando il suo tridente. Guardandolo da vari punti di vista, il Nettuno appare in posizioni sempre diverse, con la torsione nella postura e l’imponenza delle dimensioni che concretizzano l’idea di una figura in movimento. Una dinamicità e un’eleganza che nei secoli hanno influenzato l’attività di numerosi artisti. Tra questi figura anche il pittore Mario Maserati, che si ispirò proprio al tridente di Nettuno per dare vita al simbolo della casa automobilistica fondata a Bologna nel 1914 dal fratello Alfieri, sottolineando il forte legame con la città attraverso l’utilizzo dei colori rosso e blu che caratterizzano rispettivamente il tridente e lo sfondo della scritta Maserati. Fedele alla statua che ha ispirato il proprio stemma, Maserati è da sempre un simbolo d’eccellenza capace di coniugare sportività ed eleganza elevando questi aspetti ai massimi livelli. La dinamicità intesa come capacità di innovare e di rinnovarsi continuamente rappresenta dunque un elemento cardine nella filosofia della Casa del Tridente. Ne è un concreto esempio la sfida che il costruttore ha deciso di affrontare investendo nella digitalizzazione dello stabilimento “Avvocato Giovanni Agnelli Plant” (AGAP) di Grugliasco (TO).
Nel segno della tradizione
Ad oggi la società suddivide la propria produzione all’interno di tre differenti stabilimenti: a Mirafiori dispone di una linea dedicata a Levante, il primo SUV nella storia del costruttore emiliano; nella sede storica di Modena vengono prodotte GranTurismo e GranCabrio; Ghibli e la nuova Quattroporte invece nascono nello stabilimento di Grugliasco. “Fino a qualche anno fa la produzione di Maserati era interamente affidata alla sede di Modena, dove le vetture venivano realizzate in modo completamente artigianale. – esordisce Ennio Meccia, Responsabile del Plant di Grugliasco – Si trattava quindi di una produzione di nicchia con volumi ridotti. Negli ultimi anni però l’ingresso dello stabilimento di Grugliasco nel progetto Maserati ha portato a una profonda revisione del processo produttivo, supportata da importanti investimenti che hanno reso tecnologicamente all’avanguardia il plant torinese”. La sfida affrontata dalla Casa del Tridente è a dir poco impegnativa, poiché al notevole incremento del numero di unità prodotte si affianca la necessità di mantenere inalterati gli altissimi standard qualitativi che da sempre contraddistinguono le auto del marchio emiliano. Il tutto senza dimenticare uno dei principali aspetti per il quale il brand è apprezzato su scala mondiale: l’altissima possibilità di customizzazione delle vetture. Per avere un’idea del livello personalizzazione offerto, basti pensare che per il modello Quattroporte sono possibili circa 800.000 miliardi di combinazioni diverse considerando tutti gli optional, le versioni, i colori e gli interni disponibili.
“A nostro parere la digitalizzazione del processo e del prodotto è la strada da percorrere per affrontare con successo queste sfide, e i risultati che stiamo ottenendo lo dimostrano. – prosegue Meccia – Il processo di ammodernamento della produzione e dello stabilimento AGAP ci ha permesso di mantenere gli elevati standard in termini di qualità e di personalizzazione della vettura nel contesto di una produzione industriale, senza dimenticare le origini di un prodotto quasi artigianale soprattutto in termini di valore aggiunto e orgoglio per il prodotto espresso dalle persone che realizzano una Maserati”.
Condividere il know-how
Volumi elevati e customizzazione spinta si traducono in una grande mole di informazioni da dover gestire e utilizzare nel modo corretto. Inviare alla persona giusta una determinata informazione nell’esatto momento in cui ne ha bisogno rappresenta infatti la chiave per velocizzare la produzione riducendo il time to market e il rischio di errori. In quest’ottica all’interno dello stabilimento di Grugliasco è stato adottato uno strumento informatico che consente di condividere su un’unica piattaforma sia il design del prodotto sia il design del processo che andrà a generare quello specifico prodotto. “Attraverso tale strumento possiamo creare quello che noi chiamiamo digital twin, ovvero un gemello digitale del modello reale sul quale effettuiamo simulazioni di varia natura. – spiega Giuseppe Bramante, ICT – Head of Manufacturing, Supply Chain & Product Configuration in Maserati – L’opportunità di simulare in anticipo qualsiasi processo e di verificare l’effetto di modifiche significative al processo all’interno di un ambiente virtuale condiviso con tutti i reparti e con partner esterni che forniscono porzioni delle linee produttive ci permette di avere un riscontro di eventuali problemi prima di realizzare il modello fisico. Modificare il digital twin è più semplice e veloce rispetto al modificare il gemello reale, e grazie a questa possibilità siamo in grado di ridurre in modo consistente il time to market”. Lo strumento prettamente informatico è stato accompagnato da un processo che ha radicalmente cambiato l’approccio ai nuovi progetti. “In passato le varie fasi del ciclo produttivo avvenivano affrontate in sequenza e a compartimenti stagni, per così dire. – continua Bramante – Le persone operavano esclusivamente all’interno delle proprie aree di competenza rendendo la comunicazione tra i reparti lenta e inefficace. Oggi invece riuniamo fisicamente attorno allo stesso tavolo persone con competenze differenti ma legate allo stesso processo. Competenze legate al prodotto, al processo, alla logistica e a molti altri aspetti vengono quindi condivise in modo semplice e rapido, in modo da avere una visione a 360° del progetto che si sta seguendo”. La condivisione fisica e informatica dei vari know how ha permesso una riduzione delle tempistiche di produzione, ma soprattutto ha creato uno strumento che è vivo e che viene impiegato per gestire giorno dopo giorno tutte le attività del plant nel modo più efficiente possibile.
WPI e WCM
La riduzione del time to market è solo uno dei vantaggi derivanti dall’utilizzo dell’approccio integrato alla produzione. “Questo nuovo modo di produrre, che nel nostro gergo chiamiamo WorkPlace Integration (WPI), ci consente di verificare e migliorare ogni aspetto della produzione grazie al gemello virtuale. – afferma Bramante – Tra i temi sui quali abbiamo investito maggiormente figura l’ergonomia, che consente all’operatore di lavorare nelle migliori condizioni possibili e di raggiungere risultati ottimali in termini di qualità del prodotto. Abbiamo sviluppato anche il tema della connessione, che ci permette di trasferire i dati della configurazione del processo dal digital twin direttamente alle macchine e al plant. Il vantaggio che ne deriva è la coerenza tra le caratteristiche del prodotto che progettiamo e quello che realizziamo fisicamente”. All’interno dell’AGAP è stata sensibilmente migliorata anche la tracciabilità dei componenti, che assicura la visibilità di tutte le attività svolte sulla vettura, controlli di qualità compresi, e permette di avere a disposizione l’intera storia del veicolo aggiornata in tempo reale.
Il processo di digitalizzazione dunque ha portato cambiamenti a 360° che hanno coinvolto l’intero stabilimento a tutti i livelli e in tutti i reparti, applicando così i concetti del World Class Manufacturing (WCM). “Il WCM è un sistema basato su una metodologia strutturata, rigorosa e integrata, che copre tutti i processi dello stabilimento, dalla sicurezza all’ambiente, dalla manutenzione alla logistica, fino alla qualità. – precisa Meccia – L’obiettivo è quello di eliminare le gli sprechi, avere piena visibilità delle anomalie, azzerare le inefficienze. In generare migliorare l’efficienza del processo sotto tutti i punti di vista. In quest’ottica la digitalizzazione rappresenta uno strumento indispensabile per raggiungere tale obiettivo, poiché le metodologie utilizzate e il livello tecnologico raggiunto dalle nostre linee di produzione non possono più prescindere dall’informatizzazione dei processi”. Gli strumenti digitali adottati nello stabilimento di Grugliasco, progettati ed integrati in un’ottica Industry 4.0, dunque sono la chiave per ottimizzare i costi, snellire e velocizzare la gestione dei processi, e soprattutto per avere un controllo in tempo reale del flusso produttivo.
Supporto al personale
Il concetto che emerge e che è doveroso sottolineare è che la diffusione e l’utilizzo di questi strumenti digitali non sostituisce l’operato delle persone, ma piuttosto fornisce un valido supporto e contribuisce a migliorare la qualità delle informazioni necessarie a portare a termine in modo corretto una determinata fase del processo. “Uno degli elementi che caratterizzano il nostro marchio è la forte componente di personalizzazione della vettura. – continua Meccia – Questo significa che il nostro personale deve portare a termine un numero di operazioni decisamente elevato se lo si confronta con produzioni più standardizzate. Inoltre la customizzazione spinta porta a dover eseguire determinate operazioni in modo differente in base alle caratteristiche richieste dal prodotto finito. Di conseguenza è estremamente importante riuscire a dare all’operatore l’informazione giusta al momento giusto, che non riguarda solo la tipologia di componenti da installare sulla vettura che sta transitando in quel momento nella sua postazione, ma suggerisce anche gli strumenti da utilizzare e il modo in cui determinate operazioni devono essere portate a termine”.
La componente umana rimane quindi un elemento fondamentale all’interno dello stabilimento di Grugliasco, e come tutti gli altri fattori coinvolti dal cambio di strategia ha dovuto evolversi per adeguarsi alle nuove metodologie di produzione. “La sfida più importante e che ha dato maggiori soddisfazioni è stato il coinvolgimento di tutte le figure dell’AGAP in questo processo di digitalizzazione. – afferma Meccia – Il personale dello stabilimento ha un’età media di 47 anni, perciò si parla di persone tendenzialmente poco abituate a utilizzare strumenti digitali come pc o smartphone per il recupero di informazioni. Di conseguenza abbiamo dovuto apportare un importante cambiamento nella mentalità delle persone e nel modo di interagire con i vari strumenti, e posso dire con soddisfazione che questo change management è stato portato a termine con successo grazie anche al senso di appartenenza del personale, che si è messo in gioco affrontando nuove sfide con l’obiettivo di migliorarsi e di realizzare un prodotto sempre migliore, in pieno stile Maserati”. La nuova strategia aziendale quindi ha fatto emergere l’esigenza di nuove competenze nel personale. Alle conoscenze legate agli ambiti meccanico ed elettronico si sono infatti aggiunte l’informatica e la capacità di adattarsi alle nuove metodologie di produzione. Il tutto porta a figure professionali con competenze trasversali, che si dimostrano in linea con la volontà del costruttore di migliorare l’integrazione tra i vari reparti dello stabilimento torinese.
Partner integrati
Approccio, metodologie, strumenti, processi, prodotti, personale. Il cambiamento in atto ha coinvolto tutto questi fattori controllati direttamente da Maserati. Perché la nuova filosofia abbia successo però è necessaria anche la collaborazione da parte di un elemento esterno: i fornitori. “Nella nostra attività ci avvaliamo della collaborazione di circa 230 fornitori principali, il 70% dei quali si trova in un raggio di meno di 200 km di distanza dall’AGAP. – prosegue Meccia – La vicinanza è un elemento fondamentale per ridurre i costi logistici e per avere tempi di reazione migliori a fronte di eventuali variazioni d’ordine. L’altro fattore di primaria importanza riguarda l’integrazione all’interno del nostro processo produttivo. In questo contesto i nostri fornitori sono cresciuti insieme a noi per migliorare i flussi e la qualità delle informazioni scambiate, con l’obiettivo di rendere l’intera produzione più flessibile e più rapida. Grazie ai nuovi strumenti informatici adottati da entrambe le parti, siamo in grado di inviare le nostre richieste e ricevere costanti aggiornamenti in merito all’avanzamento delle loro attività. Così facendo possiamo seguire il loro operato fino alla consegna del materiale nel nostro stabilimento, e possiamo intervenire in tempi rapidi per risolvere eventuali problemi”.
Mai fermarsi!
La digitalizzazione dunque ha portato una serie di vantaggi alla produzione Maserati. Ad ogni modo, fedele alla tradizione che la identifica come azienda votata all’innovazione, la Casa del Tridente sta già lavorando ad altre soluzioni per migliorare ulteriormente prodotti e processi. “Uno dei temi caldi è la mobility all’interno del plant. – conferma Bramante – La presenza di touch screen fissi nelle postazioni complica la spaghetti chart, ovvero lo schema dei movimenti che l’operatore deve compiere per recuperare le informazioni. Una potenziale soluzione è rappresentata dai wearable devices, strumenti digitali che la persona può indossare e dai quali può ricevere informazioni senza compiere movimenti inutili. Un’altra area sulla quale stiamo lavorando è il 3D printing, quindi la possibilità di utilizzare stampanti con tecnologia additiva per la produzione di strumenti di supporto per la produzione e manutenzione dell’impianto.”.
a cura di Davide Davò
Condividi l'articolo
Scegli su quale Social Network vuoi condividere